Key Considerations for Tungsten Carbide Component Machining and Future Prospects
Tungsten carbide, renowned for its exceptional hardness, wear resistance, and heat resistance, has found widespread application in various industrial sectors. However, its unique properties also impose higher requirements on the […]
Tungsten carbide, renowned for its exceptional hardness, wear resistance, and heat resistance, has found widespread application in various industrial sectors. However, its unique properties also impose higher requirements on the machining process. This article comprehensively analyzes the key points to be considered in the machining of tungsten carbide components and looks forward to future developments.
In terms of material selection, different tungsten carbide materials vary in composition, hardness, and wear resistance, and must be chosen based on specific application scenarios and requirements. Additionally, the purity and quality of the material are crucial to avoid impurities affecting the machining quality and product performance. Prior to machining, tungsten carbide materials must undergo pretreatment steps such as heat treatment, cutting, and grinding to lay a solid foundation for subsequent processing.
O nosso negócio de fábrica: peças de metal duro, peças de molde, moldes de injeção médica, moldes de injeção de precisão, moldagem por injeção de teflon PFA, acessórios para tubos PFA. e-mail: [email protected],whatsapp:+8613302615729.
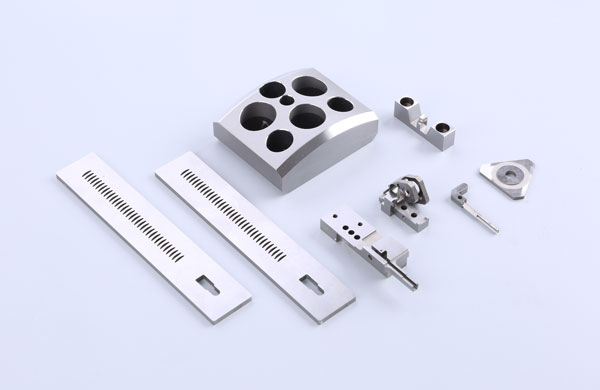
The choice of machining equipment and tools is equally critical. For high-precision components, high-precision CNC machines, electrical discharge machines (EDM), and other equipment are necessary. In terms of tool selection, high-hardness, high-wear-resistance tools such as cemented carbide cutters and diamond abrasives are preferred. Furthermore, appropriate cutting parameters and machining methods must be selected based on machining requirements to ensure a smooth process.
During machining, it is essential to strictly control cutting force and temperature to prevent tool wear and decreased machining accuracy. Simultaneously, maintaining machining stability is crucial, requiring the selection of suitable fixtures and support methods to ensure workpiece stability. Moreover, safety operations cannot be ignored, and safety procedures must be strictly followed, with the use of protective equipment.
After machining, tungsten carbide components must undergo cleaning, deburring, and other treatments, followed by various quality inspections to ensure compliance with design requirements.
Looking ahead, with technological advancements and industrial development, tungsten carbide component machining technology will continue to innovate and improve. This will contribute to the sustained development and progress of the industry, providing high-quality tungsten carbide component products for more sectors.
Publicações relacionadas
- Peças em carboneto de tungsténio: A pérola brilhante do fabrico industrial
- As aplicações generalizadas do carboneto de tungsténio
- Análise exaustiva das peças em carboneto de tungsténio: Caraterísticas, tipos, aplicações e tendências futuras
- Análise exaustiva dos componentes de carboneto de tungsténio