Análise do punção de carboneto de tungsténio: Uma exploração da dureza do material em peças de desgaste com formato especial de carboneto de tungsténio
The performance of tungsten carbide special-shaped wear parts is often closely related to their material hardness. Generally, as the material hardness increases, so does its wear resistance; similarly, an improvement […]
The performance of tungsten carbide special-shaped wear parts is often closely related to their material hardness. Generally, as the material hardness increases, so does its wear resistance; similarly, an improvement in bending strength leads to enhanced impact toughness. However, an increase in material hardness often comes at the expense of reduced bending strength and impact toughness. High-speed steel, with its excellent bending strength, impact toughness, and good machinability, remains the most widely used tool material, followed by cemented carbide.
Cubic boron nitride excels in cutting high-hardness hardened steel, hard cast iron, and other materials; polycrystalline diamond is more suitable for cutting non-ferrous metals, alloys, plastics, and fiberglass. Carbon tool steel and alloy tool steel are now primarily used for making hand tools such as files, dies, and taps.
O nosso negócio de fábrica: peças de metal duro, peças de molde, moldes de injeção médica, moldes de injeção de precisão, moldagem por injeção de teflon PFA, acessórios para tubos PFA. e-mail: [email protected],whatsapp:+8613302615729.
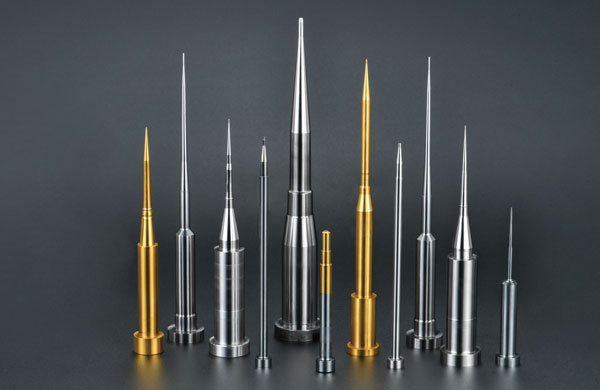
Tungsten carbide bushings (i.e., cemented carbide bushings) are renowned for their high hardness, excellent wear resistance, good strength and toughness, outstanding heat resistance, and corrosion resistance. Particularly noteworthy is their high hardness and wear resistance, which remain stable even at temperatures of 500°C and maintain a considerable level of hardness at 1000°C.
Below are several practical application cases of tungsten carbide punches:
- Tungsten Carbide Punch Stretching Die Cavity (Specifications: ∮180∮9540): Suitable for stretching 1.5mm thick cold-rolled sheet metal cylinders in metalworking factories. Its high hardness and low friction coefficient ensure a smooth, scratch-free surface on the stretched products, with a service life of up to 1.5 million cycles.
- Tungsten Carbide Punch Straight Bushing (Inner Diameter ≥ Φ1.0): Used as a lower die insert in continuous stretching dies for electronic and metalworking factories. Its high hardness and smooth inner wall result in a smooth, scratch-free surface on the stretched products, with a service life exceeding 1 million cycles.
- Integral Bushing: Designed for stretching integral bushings in metalworking and electronic factories, effectively solving the issue of narrow step distances in continuous dies.
- Special-Shaped Bushing (Elliptical or Square Inner Diameter): Suitable for continuous die inserts in electronic and metalworking factories. Its high hardness and excellent inner wall finish ensure high-quality surfaces and long service life for the stretched products, making it ideal for mass production.
- Tin-Coated Bushing: Tailored for specific needs in metalworking and electronic factories, the Tin coating enhances the smoothness and durability of the tungsten carbide bushing.
When selecting tungsten carbide special-shaped wear parts, it is crucial to choose the appropriate cemented carbide grade. The cemented carbide grades currently used in mining tools are designed based on thorough research into the characteristics of cemented carbide and its wear behavior. Years of production practice have proven their rationality. Therefore, when selecting cemented carbide grades, it is essential to consider the specific application of the alloy inserts fully.