Mirror Polishing of Tungsten Carbide Dies
1. Introduction Tungsten carbide dies, renowned for their exceptional hardness, wear resistance, and heat resistance, play a pivotal role in industrial manufacturing. However, these dies’ surface quality directly impacts the […]
1. Introduction
Tungsten carbide dies, renowned for their exceptional hardness, wear resistance, and heat resistance, play a pivotal role in industrial manufacturing. However, these dies’ surface quality directly impacts the final products’ appearance and precision. Therefore, achieving a mirror-like finish through polishing is essential to enhancing die quality. This article provides a detailed overview of the mirror polishing process for tungsten carbide molds, covering pre-polishing preparation, selection of polishing techniques, step-by-step procedures, and post-polishing treatments.
2. Pre-Polishing Preparation
- Die Cleaning
Before mirror polishing, thorough cleaning of the tungsten carbide die is necessary to remove oil, rust, and other impurities. Use cleaning agents or solvents in conjunction with soft cloths or brushes. For stubborn stains, ultrasonic cleaning or high-pressure water jetting (8-10 MPa) can be employed. - Die Inspection
After cleaning, conduct a comprehensive inspection of the die, including dimensions, shape, and surface quality. Pay special attention to defects such as cracks or pits, as these can severely affect polishing outcomes. Repair or replace any identified defects promptly. - Polishing Tool Preparation
Select appropriate polishing tools based on the die material and polishing requirements. Common tools include polishing wheels, polishing cloths, and polishing pastes. When choosing polishing wheels, consider factors such as material, grit size, and hardness. Polishing cloths should be selected based on the type of polishing wheel and polishing paste. For polishing pastes, opt for suitable types and concentrations according to the polishing requirements.
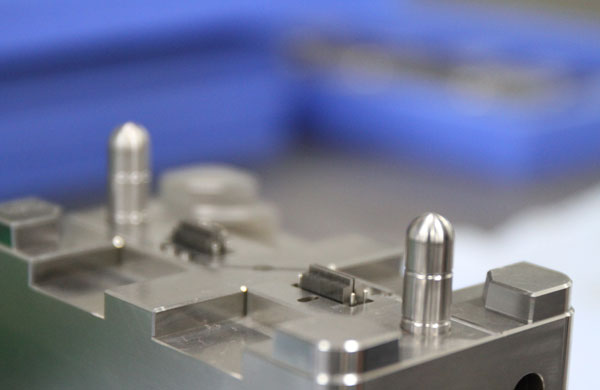
3. Selection of Polishing Techniques
There are multiple methods for mirror polishing 炭化タングステン dies, including mechanical polishing, chemical polishing, and electrolytic polishing. Each method has distinct characteristics and applications, necessitating selection based on specific scenarios.
当社の工場事業:超硬部品、金型部品、医療用射出成形金型、精密射出成形金型、テフロンPFA射出成形、PFAチューブ継手。電子メール:[email protected],whatsapp:+8613302615729。
Technique | Principle | メリット | 制限事項 | Applicable Scenarios |
---|---|---|---|---|
Mechanical Polishing | Physical abrasion to remove material | Simple operation, low cost | Prone to inducing stress layers | Preliminary rough polishing, non-mirror finishes |
Chemical Polishing | Chemical corrosion of the surface | High efficiency, uniform surface | High corrosion risk | Pre-treatment of complex cavities |
Electrolytic Polishing | Anodic oxide film stripping | Excellent mirror finish, stress-free | High equipment investment | Final polishing of precision molds |
Recommended Approach: Combine mechanical rough polishing with electrolytic fine polishing to balance efficiency and effectiveness.
4. Standardized Polishing Procedures
- Rough Polishing Stage
- Parameter Control: Pressure 0.3-0.5 MPa, rotational speed 1500-2000 rpm, duration 10-15 minutes.
- Effect Verification: Achieve a surface roughness (Ra) of ≤3.2 μm.
- Intermediate Polishing Stage
- Tool Switch: Use a wool wheel (600# grit) with aluminum oxide polishing paste.
- Process Monitoring: Check surface roughness every 5 minutes to prevent over-polishing.
- Fine Polishing Stage
- Final Treatment: Employ a silk wheel (5000# grit) with nano-diamond paste (0.02 μm).
- Environmental Requirements: Class 10,000 cleanroom, temperature 22±2°C, humidity 50%±5%.
- Acceptance Criteria: Ra ≤0.01 μm, glossiness ≥120 Gu, free of scratches or orange peel effects.
5. Post-Polishing Treatments
- Cleaning and Drying
- Cleaning Process: Rinse with deionized water, followed by 5 minutes of ultrasonic cleaning with anhydrous ethanol, and finally dry with nitrogen.
- Rust Prevention: Apply a water-based rust inhibitor (e.g., WD-40 Professional) to form a protective film.
- Long-Term Maintenance
- Storage Conditions: Store in a constant temperature and humidity cabinet (20°C, 40% humidity), avoiding direct sunlight.
- Regular Inspection: Use white light interferometry to check surface morphology monthly and remeasure roughness quarterly.
6. Safety and Efficiency Optimization Suggestions
- Safety Precautions
- Wear dust masks (N95 grade), safety goggles, and cut-resistant gloves.
- Ensure proper grounding during electrolytic polishing to prevent electrical hazards.
- Efficiency Enhancements
- Introduce automated polishing equipment (e.g., ABB robotic polishing units) to reduce human error.
- Establish a process database to record optimal parameters for different mold materials and shapes.
7. Conclusion
Achieving a mirror finish on tungsten carbide molds requires meticulous control throughout the entire process, from preparation and technique selection to maintenance. By adhering to standardized procedures and precise management, a surface roughness of Ra ≤0.01 μm can be achieved, significantly enhancing mold lifespan and product yield. Enterprises should flexibly combine polishing techniques based on their specific needs while strengthening safety training and equipment investment to drive the polishing process toward intelligence and sustainability.