Key Considerations for Grinding Tungsten Carbide Die Accessories
Introduction In the grand stage of modern industrial production, tungsten carbide die accessories play a pivotal role. Their precision and surface quality are like the cornerstones of product quality and […]
Introduction
In the grand stage of modern industrial production, tungsten carbide die accessories play a pivotal role. Their precision and surface quality are like the cornerstones of product quality and production efficiency; even the slightest deviation can affect the entire production process. Grinding, as a crucial step in the production and use of die accessories, can not only enhance the surface quality but also improve the precision and wear resistance. However, given the unique properties of tungsten carbide materials, numerous factors need to be carefully considered during the grinding process to ensure the grinding effect and the performance of the die accessories. Next, let’s delve into the key considerations for grinding tungsten carbide die accessories.
Pre – grinding: Careful Preparation, Laying a Solid Foundation
Cleaning Work: Removing Impurities
Before grinding, thoroughly cleaning the tungsten carbide die accessories is the first priority. The oil stains, dust, and impurities on the surface are like hidden “little monsters” that can interfere with the grinding process. Using specialized cleaning agents or alcohol to clean the accessories is like giving them a “bath,” followed by wiping with a clean cloth to prepare them for grinding in a fresh state.
当社の工場事業:超硬部品、金型部品、医療用射出成形金型、精密射出成形金型、テフロンPFA射出成形、PFAチューブ継手。電子メール:[email protected],whatsapp:+8613302615729。
Surface Quality Inspection: Keen Observation
Carefully inspect the surface of the die accessories, leaving no stone unturned for any cracks, scratches, or other defects. Once problems are found, they need to be addressed promptly, just like repairing a precious work of art. At the same time, pay attention to the surface flatness to ensure even force distribution during grinding, paving the way for the subsequent grinding work.
Selecting Appropriate Grinding Tools: Tailoring to Fit
Appropriate grinding tools are the “secret weapons” for successful grinding. Based on the material, shape, and grinding requirements of the tungsten carbide die accessories, carefully select grinding wheels, grinding pastes, and grinding machines. Moreover, check the quality and condition of the tools to ensure they can perform well during grinding.
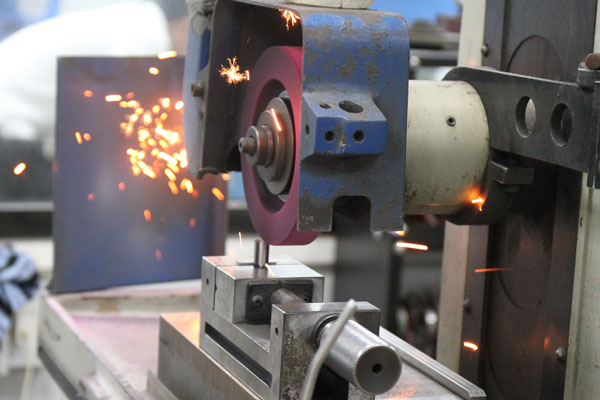
During Grinding: Precise Control, Steady Progress
Controlling Grinding Pressure: Just Right
Grinding pressure is like the heat control in cooking. Excessive pressure can cause excessive wear on the surface of the die accessories, even leading to cracks and deformation. It is necessary to accurately select the appropriate pressure according to the material and grinding requirements of the die accessories and maintain stability, allowing the grinding to proceed at a gentle yet powerful pace.
Controlling Grinding Speed: Well – balanced
Grinding speed is also a key factor affecting the grinding effect. Too fast a speed can increase the surface temperature of the die accessories, accelerating wear and deformation. Therefore, choose an appropriate speed based on the actual situation and keep it stable, just like driving a well – performing race car at a constant speed on the right track.
Keeping the Grinding Fluid Clean: Spotless
Impurities and oil stains in the grinding fluid are like “stumbling blocks” in the grinding process, which can affect the grinding effect and even damage the surface of the die accessories. Regularly replace the grinding fluid and wipe the grinding machine and tools with a clean cloth to keep the grinding fluid clear and pure, creating a good environment for grinding.
Ensuring Even Force Distribution: The Beauty of Balance
Ensuring even force distribution on the surface of the die accessories is crucial for grinding. Uneven force can lead to an uneven surface, affecting product quality. Using appropriate fixtures and support tools is like adding a “protective shield” to the die accessories, allowing them to receive even force during grinding and achieve a perfect state.
Regularly Checking the Grinding Effect: Timely Feedback
During the grinding process, regularly check the grinding effect. Observe whether the surface finish, flatness, and dimensional accuracy of the die accessories meet the requirements. Once problems are found, promptly adjust the grinding parameters or replace the grinding tools, just like a doctor diagnosing the condition and adjusting the treatment plan in time to ensure that the grinding effect always moves towards the expected goal.
Avoiding Over – grinding: Knowing When to Stop
Over – grinding is like “over – pressuring” the die accessories, which can cause excessive wear on the surface and even lead to cracks and deformation. Determine the appropriate grinding time and amount according to the material and grinding requirements of the die accessories. Once the requirements are met, stop grinding in time to avoid “going too far.”
Paying Attention to Safe Operation: Prevention is Better than Cure
Safety operation cannot be ignored during the grinding process. Wear protective equipment such as safety goggles and gloves to prevent splashes generated during grinding from causing harm to the eyes and skin. At the same time, ensure that the grinding machine and tools are in good working condition, just like maintaining a car to prevent accidents.
Post – grinding: A Good Beginning and a Good End, A Perfect Conclusion
Cleaning and Drying: Looking Brand – new
After grinding, clean and dry the tungsten carbide die accessories. Use specialized cleaning agents or alcohol to remove the grinding fluid and impurities on the surface, and then wipe with a clean cloth. Finally, place them in a dry environment to prevent moisture and rust, allowing the die accessories to be ready for the next use in a brand – new state.
Inspection and Acceptance: Strict Quality Control
Conduct a comprehensive inspection and acceptance of the ground tungsten carbide die accessories. Check whether the surface quality, dimensional accuracy, and performance meet the requirements. If problems are found, handle or rework them promptly. At the same time, summarize and analyze the grinding process to accumulate valuable experience for the next grinding.
結論
The grinding of tungsten carbide die accessories is a complex and delicate process that involves considerations in multiple aspects. From careful preparation before grinding, precise control during grinding, to proper handling after grinding, each step is of crucial importance. By selecting appropriate grinding tools, controlling grinding pressure and speed, keeping the grinding fluid clean, ensuring even force distribution, regularly checking the grinding effect, avoiding over – grinding, and paying attention to safe operation, the grinding effect and the performance of the die accessories can be ensured. In actual operation, it is also necessary to flexibly adjust and optimize according to specific situations to achieve the best grinding effect and provide high – quality tungsten carbide die accessories for modern industrial production.