Analysis of the Processing Methods for Tungsten Carbide Drawing Dies
Introduction In the complex process of metal wire drawing, the tungsten carbide drawing die plays a crucial and indispensable role, like a behind – the – scenes hero. Its quality […]
Introduction
In the complex process of metal wire drawing, the tungsten carbide drawing die plays a crucial and indispensable role, like a behind – the – scenes hero. Its quality serves as the cornerstone, directly determining the efficiency of wire drawing and the quality of the final product. Tungsten carbide, as a high – performance hard alloy material, boasts outstanding characteristics such as high hardness, high wear resistance, and high elastic modulus, occupying a pivotal position in the field of drawing die manufacturing. Next, let’s delve into the processing methods of tungsten carbide drawing dies and gain a comprehensive understanding of every link from material selection to inspection and quality control.
Processing Methods of Tungsten Carbide Drawing Dies
Material Selection: Laying a Solid Foundation for Quality
The material selection for tungsten carbide drawing dies is the first step in initiating high – quality die manufacturing, and its importance cannot be overstated. High – quality tungsten carbide materials need to possess uniform composition, high purity, and be free of impurities. These characteristics act as a solid foundation, providing a strong guarantee for the high hardness and wear resistance of the die. At the same time, when selecting tungsten carbide materials, thermal stability and thermal shock resistance are also crucial factors that cannot be ignored. In the high – temperature wire – drawing environment, good thermal stability and thermal shock resistance can ensure that the die remains stable and durable, like a tenacious warrior standing firm on the high – temperature battlefield.
La nostra attività in fabbrica: parti in metallo duro, parti di stampi, stampi a iniezione medicali, stampi a iniezione di precisione, stampaggio a iniezione di teflon PFA, raccordi per tubi PFA. e-mail: [email protected],whatsapp:+8613302615729.
Blank Preparation: Shaping the Preliminary Form
Blank preparation is the initial stage of tungsten carbide drawing die processing. Its quality, like the foundation of a building, directly affects the difficulty of subsequent processing and the final performance of the die. Blank preparation mainly includes steps such as material cutting, forging, and pre – processing. First, according to the specifications and size requirements of the die, the tungsten carbide material is precisely cut into appropriate blocks, which is the first step in blank preparation, similar to cutting fabric for making clothes. Then, through the forging process, the block material is processed into a blank with a preliminary shape. During the forging process, the control of parameters such as heating temperature, forging ratio, and cooling speed is of utmost importance. They act as precise regulators, ensuring the uniformity of the blank’s structure and the stability of its performance. Finally, pre – processing operations such as turning and milling are carried out on the blank to remove defects such as oxide scales and cracks generated during the forging process, laying a good foundation for subsequent processing, just like making preliminary adjustments to a painting before coloring.
Rough Machining: Sculpting the Approximate Outline
Rough machining is one of the key steps in the processing of tungsten carbide drawing dies. Its goal is to process the blank into an intermediate product with an approximate final shape and size. Rough machining mainly adopts cutting methods such as milling, turning, and drilling. During this process, strict control of parameters such as cutting allowance, cutting speed, and cutting depth is required. Excessive cutting force may cause deformation or damage to the die, just as an overly forceful stroke by a sculptor may ruin the initial shape of a work. At the same time, keeping the cutting tools sharp is also crucial for improving processing efficiency and quality. Sharp tools are like precise surgical knives, capable of more accurately removing excess material.
Finish Machining: Creating a Precise Finished Product
Finish machining is the final step in the processing of tungsten carbide drawing dies and a key step in determining the ultimate quality of the die. Its purpose is to process the intermediate product into a finished product with precise dimensions and surface quality. Finish machining mainly includes steps such as grinding, polishing, and lapping. During the grinding process, selecting the appropriate grinding wheel and grinding parameters is of great importance, as they directly affect the surface roughness and dimensional accuracy of the die. Polishing and lapping are further steps to improve the surface quality of the die, removing burrs and scratches generated during the grinding process, just like making the final touches and polishing a fine artwork. During the finish machining process, maintaining the cleanliness of the processing environment cannot be ignored, as dust and impurities can contaminate the die surface like stains, affecting the quality of the die.
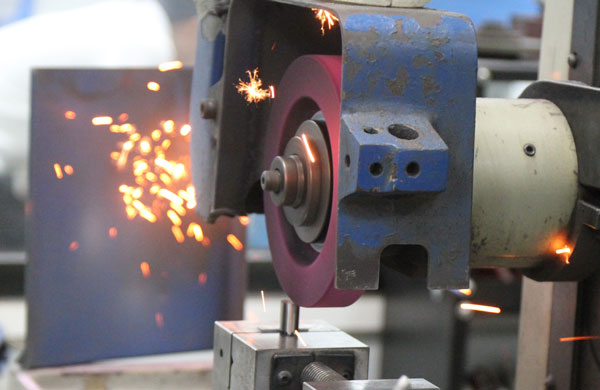
Heat Treatment: Optimizing Material Performance
Heat treatment is an indispensable step in the processing of tungsten carbide drawing dies. It is like a magical process that changes the structure and properties of the material through heating and cooling to meet the usage requirements of the die. Common heat treatment processes include quenching, tempering, and aging treatment. Quenching is the process of rapidly cooling the die after heating it to a certain temperature. This process can significantly improve the hardness and wear resistance of the die, just like putting on a hard armor for the die. Tempering is the process of heating and cooling after quenching, which can reduce the brittleness of the die and improve its toughness, enabling the die to have a certain impact resistance while maintaining high hardness. Aging treatment is the process of keeping the die at a certain temperature for a specific period to eliminate internal stress and improve the stability of the die. During the heat treatment process, strict control of parameters such as heating temperature, holding time, and cooling speed is the key to ensuring the performance and quality of the die. These parameters are like precise recipes, and any deviation may affect the final result.
Inspection and Quality Control: Ensuring Compliance with Quality Standards
Inspection and quality control are essential steps in the processing of tungsten carbide drawing dies. They act as strict gatekeepers to ensure that the quality and performance of the die meet the usage requirements. Inspection mainly includes steps such as dimensional inspection, surface quality inspection, and hardness inspection. Dimensional inspection uses various measuring tools and instruments to measure the dimensions and shape accuracy of the die, ensuring that the dimensions of the die are accurate. Surface quality inspection evaluates the quality of the die by observing its surface condition, just like checking the appearance of a product for perfection. Hardness inspection measures the hardness value of the die using a hardness tester to ensure that the die has sufficient hardness. In terms of quality control, establishing a strict quality management system and inspection system is crucial. Comprehensive inspections and acceptance of raw materials, semi – finished products, and finished products are carried out to ensure that the quality and performance of the die meet the usage requirements.
Conclusione
The processing method of tungsten carbide drawing dies is a complex process involving multiple steps. From material selection to inspection and quality control, each step is closely linked and indispensable. During the processing process, strict control of various parameters and process requirements is the key to ensuring that the quality and performance of the die meet the usage requirements. With the continuous progress of science and technology and the development of industrial production, the processing methods of tungsten carbide drawing dies will also be continuously improved and optimized to meet the requirements of higher performance and quality.
Dongguan Yize Mould, a professional tungsten carbide processing manufacturer, provides a series of high – quality products such as tungsten carbide dies, tungsten carbide processing, tungsten carbide rollers, tungsten carbide blades, hard alloys, and tungsten carbide punches. If you have relevant needs, please feel free to call +86 13302615729 (same number for WeChat and Whatsapp) for more detailed information.