Comprehensive Analysis of Tungsten Carbide Machining Considerations
Tungsten carbide, renowned for its high hardness, high wear resistance, and high thermal stability, is widely used in various industrial fields. However, its machining difficulty is relatively high. This article […]
Tungsten carbide, renowned for its high hardness, high wear resistance, and high thermal stability, is widely used in various industrial fields. However, its machining difficulty is relatively high. This article provides a comprehensive analysis of the key points to consider in tungsten carbide machining, including its machining characteristics, equipment selection, process optimization, safety norms, and quality control.
Firstly, understanding the machining characteristics of tungsten carbide is essential knowledge before machining. Although tungsten carbide has excellent properties, its brittleness and high machining difficulty can lead to issues such as cracks and chipping during the machining process.
Notre activité : pièces en carbure, pièces de moule, moules d'injection médicale, moules d'injection de précision, moulage par injection de téflon PFA, raccords de tubes PFA. email : [email protected],whatsapp:+8613302615729.
In terms of equipment selection for machining, the machine tool must have high precision and rigidity to ensure stable machining. The cutting tool should be made of cemented carbide or ceramic, with a sharp and chip-free cutting edge. The fixture should have sufficient rigidity and precision to ensure the stability of the workpiece.
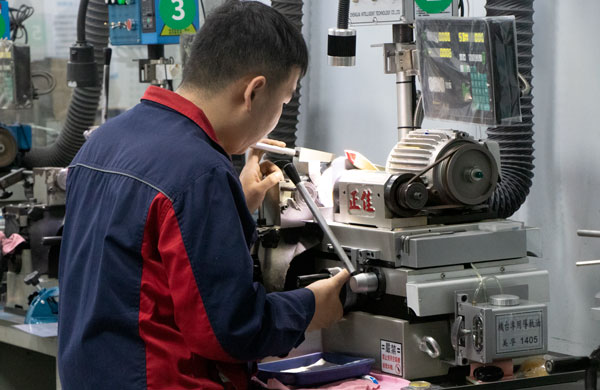
Process optimization is crucial for improving machining quality. Cutting speed, feed rate, and cutting depth need to be reasonably adjusted according to the characteristics of tungsten carbide and machining requirements. The use of coolant is also vital, as it can reduce cutting temperature, minimize tool wear, and improve the surface quality of the workpiece. In addition, the planning of the machining sequence should not be overlooked, with key areas such as datum surfaces and locating surfaces being machined first.
Machining safety is an issue that must be emphasized during tungsten carbide machining. Operators must strictly follow operating procedures, wear protective equipment, and receive professional training. Machine tools need regular inspection and maintenance to avoid overload and overspeed operations. The storage and use of cutting tools also require caution, and the machine tool power should be turned off when changing tools.
Finally, quality control is key to ensuring the success of the machining process. A comprehensive inspection of the workpiece should be conducted before machining, the quality should be monitored in real-time during machining, and post-processing such as cleaning and deburring should be carried out after machining.
In summary, tungsten carbide machining is a complex and important task that requires attention to multiple aspects to ensure machining quality and efficiency.
Articles connexes
- Comprehensive Guide to Testing Tungsten Carbide Rods: Key Steps to Ensure Quality and Performance
- Complete Guide to Tungsten Carbide Die Installation: Details Determine Success
- Key Considerations for Tungsten Carbide Component Machining and Future Prospects
- Pièces en carbure de tungstène : La perle brillante de la fabrication industrielle