Formas de reducir los defectos en el carburo de tungsteno
El carburo de tungsteno, con su extraordinaria dureza y resistencia al desgaste, ocupa una posición central en la fabricación industrial moderna. Sin embargo, como todos los materiales, el carburo de tungsteno también encuentra inevitablemente diversos defectos durante la producción [...].
El carburo de tungsteno, con su extraordinaria dureza y resistencia al desgaste, ocupa una posición central en la fabricación industrial moderna. Sin embargo, como todos los materiales, el carburo de tungsteno también encuentra inevitablemente varios defectos durante la producción y aplicación. Este artículo tiene como objetivo profundizar en los defectos comunes del carburo de tungsteno y sus causas, y proponer un amplio conjunto de estrategias para reducir los defectos, proporcionando una valiosa orientación para las prácticas de producción en las industrias relacionadas.
I. Análisis de defectos comunes en el carburo de tungsteno y sus causas
Nuestra actividad de fábrica: piezas de carburo, piezas de molde, moldes de inyección médica, moldes de inyección de precisión, moldeo por inyección de teflón PFA, accesorios de tubo PFA. correo electrónico: [email protected],whatsapp:+8613302615729.
Durante su producción y uso, el carburo de wolframio suele presentar defectos como descascarillado, poros, ampollas, deformación, corazón negro, grietas, rebabas, poros de gas y microestructura irregular. La formación de estos defectos suele atribuirse a múltiples factores, como la calidad de las materias primas, el control de los procesos de producción y el estado de los equipos.
- Peeling: Se origina por el efecto de contacto del cobalto en el compacto, lo que provoca la descomposición de los gases que contienen carbono en carbono libre, debilitando la resistencia local del compacto y provocando posteriormente el pelado.
- Poros: Se refiere a poros mayores de 40 micrómetros, causados principalmente por impurezas en el cuerpo sinterizado que no son humedecidas por el metal disolvente o por una segregación severa de las fases sólida y líquida.
- Blistering: Es el resultado del aire atrapado en el cuerpo sinterizado que no puede expulsarse, o de reacciones químicas dentro del cuerpo sinterizado que generan grandes cantidades de gas, lo que da lugar a superficies convexas en el carburo de wolframio, afectando a su rendimiento.
- Deformación: Como la formación de ampollas y la deformación cóncava, causadas principalmente por una distribución desigual de la densidad en el compacto, una deficiencia local de carbono en el cuerpo sinterizado, una carga inadecuada en la nave de sinterización o unas placas de soporte desiguales.
- Corazón negro: Se refiere a la microestructura suelta en la fractura de la aleación, resultante de un contenido de carbono demasiado bajo o demasiado alto.
- Grietas: Común durante la sinterización, debido a la relajación de la presión en el compacto durante el secado que no es inmediatamente aparente, la rápida recuperación elástica durante la sinterización, o la oxidación severa de parte del compacto que conduce a una expansión térmica diferente entre las zonas oxidadas y no oxidadas.
- Fresas: Sustancias en forma de partículas que aparecen en los bordes o superficies de los productos, afectando a su aspecto y calidad, posiblemente causadas por cuchillas de corte anormales o dañadas, pulido inadecuado o procesos incorrectos.
- Poros de gas: Poros o burbujas en el interior o en la superficie de los productos, que reducen la densidad y la resistencia, posiblemente debido a un contenido excesivo de gas en las materias primas, a defectos en el proceso de prensado o a parámetros inadecuados del horno de sinterización.
- Microestructura irregular: Presencia de regiones laminares o porosas en los productos, lo que da lugar a una microestructura desigual, posiblemente debida a temperaturas de reacción desiguales, tiempos de reacción insuficientes o excesivos, o parámetros de prensado inadecuados.
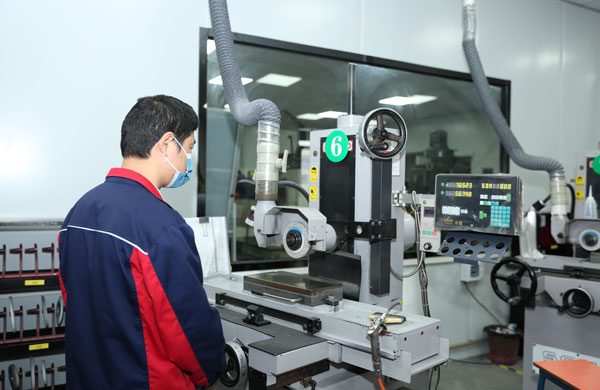
II. Estrategias integrales para reducir los defectos en el carburo de tungsteno
Para abordar los defectos mencionados y sus causas, se pueden aplicar las siguientes estrategias para reducir eficazmente la aparición de defectos:
- Selección de materiales y control de calidad: Seleccionar materias primas de alta calidad, controlar estrictamente el contenido de impurezas y reforzar la inspección de calidad para garantizar que las materias primas cumplen las normas de producción.
- Optimización de los procesos de producción: Adaptar los parámetros adecuados del proceso, como la fuerza de prensado, la temperatura de sinterización y el tiempo de mantenimiento, en función de las características del producto. Reforzar el control del proceso para garantizar la estabilidad y coherencia de los parámetros.
- Mantenimiento y modernización de equipos: Mantener regularmente los equipos de producción para garantizar su funcionamiento normal. Manténgase al día de las nuevas tecnologías y los avances de los equipos, y actualícelos oportunamente para mejorar la eficacia de la producción y la calidad de los productos.
- Mejora de la formación de los empleados: Reforzar la formación técnica y la concienciación sobre la calidad de los empleados, mejorando sus competencias técnicas. Garantizar que los empleados dominan los procesos de producción y las normas operativas, reduciendo el impacto de los factores humanos en la calidad del producto.
- Estricta inspección de calidad: Establecer un sólido sistema de inspección de la calidad, realizar inspecciones estrictas de las distintas fases de producción. Analizar y tratar con prontitud los productos defectuosos, identificar las causas y tomar las medidas de mejora correspondientes.
- Introducción de tecnologías avanzadas: Introducir activamente tecnologías avanzadas como el proceso de rectificado electrolítico y técnicas de medición de alta precisión para mejorar la precisión de la producción y la calidad del producto de carburo de tungsteno.
En resumen, la reducción de defectos en el carburo de wolframio requiere una consideración exhaustiva de múltiples aspectos, como la selección de materiales, los procesos de producción, los equipos, los empleados, la inspección de calidad y la introducción de tecnologías avanzadas. Sólo mediante un enfoque holístico se pueden reducir eficazmente los defectos, mejorando así la calidad del producto y la competitividad.
Entradas relacionadas
- ¿Cómo mejorar la eficiencia de trabajo de las matrices de carburo de tungsteno?
- Análisis exhaustivo de los tipos de carburo de wolframio
- Explorando las ventajas del carburo de tungsteno: Excelente resistencia a la corrosión
- Exploración de las principales características de los moldes de carburo de tungsteno