Analyse der Unterschiede zwischen inländischen und importierten Hartmetallstempeln
Derzeit lässt sich der heimische Markt für Hartmetallstempel je nach Materialqualität und Nutzeranforderungen in die Kategorien Low-End, Mid-End und High-End unterteilen. Auf dem Low-End-Markt werden die Formen von [...]
Currently, the domestic tungsten carbide punch market can be segmented into low-end, mid-end, and high-end categories based on material quality and user requirements.
In the low-end market, molds used by daily hardware and plastic products manufacturers predominate. These enterprises have no special requirements for tungsten carbide punches and primarily seek low costs.
Unser Fabrikgeschäft: Hartmetallteile, Formteile, medizinische Spritzgussformen, Präzisionsspritzgussformen, Teflon-PFA-Spritzguss, PFA-Rohrverschraubungen. E-Mail: [email protected],whatsapp:+8613302615729.
The mid-end market is dominated by domestic medium-sized mold manufacturing enterprises. These enterprises have stricter requirements for tungsten carbide punches, emphasizing stable material quality and moderate prices. They mostly use domestic tungsten carbide punches, which are priced at approximately one-third of imported products.
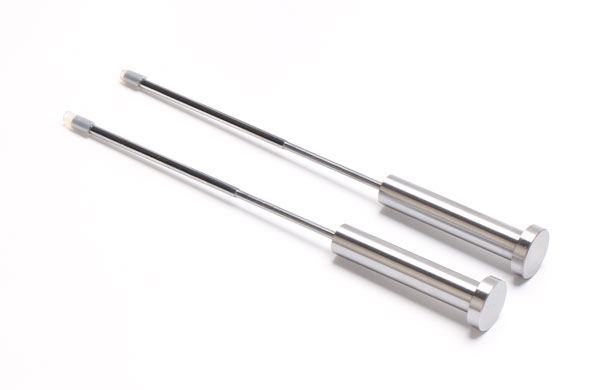
The high-end market is led by foreign-invested and export-oriented mold manufacturing enterprises. These enterprises have high-quality requirements for tungsten carbide punches, so they mostly choose imported products, with only a small amount using domestic high-quality materials. The price of imported tungsten carbide punches is usually about twice that of domestic products.
In the high-end market, a crucial segment, the market share of domestic tungsten carbide punches remains low. However, this market represents the development trend of the domestic mold industry and holds great potential.
According to market research conducted by Gaolue Precision Mold Company, domestic tungsten carbide punches do indeed lag behind their foreign counterparts. The quality of domestic tungsten carbide punches fails to meet the ASTM A681 standard, only reaching the international average level. For the stringent requirements put forward by high-standard users, domestic products currently cannot meet the demand.
Furthermore, steel for plastic molds must have a high-gloss surface, corrosion resistance, wear resistance, high thermal conductivity, good machinability, polishability, and etching performance. Domestic steel falls short in these aspects, with a service life of only about half that of foreign products. Steel quality is one of the key factors contributing to this situation.