What are the processing conditions for Tungsten Carbide bushings?
Tungsten Carbide bushings, serving as indispensable accessories for stamping dies, are classified as replaceable die consumables. Made from special mold steels, Tungsten Carbide bushings can be designed into various shapes […]
Tungsten Carbide bushings, serving as indispensable accessories for stamping dies, are classified as replaceable die consumables. Made from special mold steels, Tungsten Carbide bushings can be designed into various shapes to meet production needs. Depending on material, shape, and application, Tungsten Carbide bushings are primarily categorized into SKD, SKH, ASP Tungsten Carbide, thread-drawing Tungsten Carbide, hexagonal Tungsten Carbide, special-shaped Tungsten Carbide, and high-speed steel Tungsten Carbide, among others.
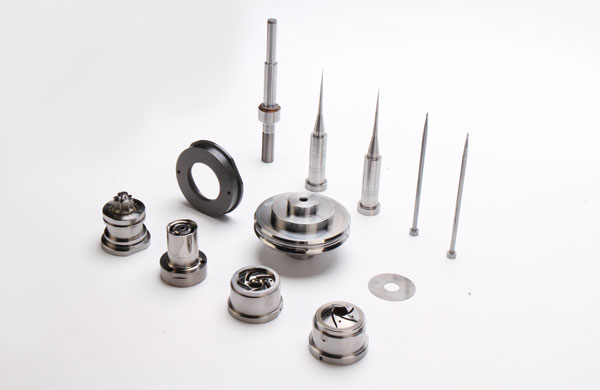
- During the processing of Tungsten Carbide bushings, it should be ensured that the workpiece makes uniform contact with the entire surface of the abrasive tool. This ensures uniform loading and wear on the abrasive tool’s surface, maintaining its surface precision over time.
- The processing should guarantee uniform grinding of the workpiece, meaning every point on the workpiece surface receives the same amount of grinding. This is crucial for ensuring the geometric accuracy and dimensional uniformity of the workpiece.
- The processing path should be continuously and regularly changed in direction to avoid premature repetition. This allows the numerous cutting marks on the workpiece surface to intersect and cancel each other out in a regular pattern, resulting in a smoother surface and improved surface quality of the workpiece.
- The grinding process for Tungsten Carbide bushings should select the optimal operating speed based on specific grinding requirements. For grinding long, large-sized workpieces, low-speed grinding should be chosen; whereas for small-sized or low-precision workpieces, medium- or high-speed grinding should be selected to enhance production efficiency.