Ways to Reduce Defects in Tungsten Carbide
Tungsten carbide, with its outstanding hardness and wear resistance, occupies a pivotal position in modern industrial manufacturing. However, like all materials, tungsten carbide also inevitably encounters various defects during production […]
Tungsten carbide, with its outstanding hardness and wear resistance, occupies a pivotal position in modern industrial manufacturing. However, like all materials, tungsten carbide also inevitably encounters various defects during production and application. This article aims to delve into the common defects of tungsten carbide and their causes, and propose a comprehensive set of strategies to reduce defects, providing valuable guidance for production practices in related industries.
I. Analysis of Common Defects in Tungsten Carbide and Their Causes
Our factory business: carbide parts, mold parts, medical injection molds, precision injection molds, teflon PFA injection molding, PFA tube fittings. email: [email protected],whatsapp:+8613302615729.
During production and use, tungsten carbide often exhibits defects such as peeling, pores, blistering, deformation, black heart, cracks, burrs, gas pores, and uneven microstructure. The formation of these defects is often attributed to multiple factors, including the quality of raw materials, control of production processes, and equipment status.
- Peeling: Originates from the contact effect of cobalt in the compact, leading to the decomposition of carbon-containing gases into free carbon, weakening the local strength of the compact, and subsequently causing peeling.
- Pores: Refers to pores larger than 40 micrometers, primarily caused by impurities in the sintered body that are not wetted by the solvent metal or severe segregation of solid and liquid phases.
- Blistering: Results from air trapped within the sintered body that cannot be expelled, or chemical reactions within the sintered body that generate large amounts of gas, leading to convex surfaces on the tungsten carbide, affecting its performance.
- Deformation: Such as blistering and concave deformation, mainly caused by uneven density distribution in the compact, local carbon deficiency in the sintered body, improper loading in the sintering boat, or uneven support plates.
- Black Heart: Refers to loose microstructure in the fracture of the alloy, resulting from either too low or too high carbon content.
- Cracks: Common during sintering, due to pressure relaxation in the compact during drying that is not immediately apparent, rapid elastic recovery during sintering, or severe oxidation of part of the compact leading to different thermal expansion between oxidized and non-oxidized areas.
- Burrs: Particle-like substances appearing on the edges or surfaces of products, affecting appearance and quality, possibly caused by abnormal or damaged cutting blades, inadequate polishing, or improper processes.
- Gas Pores: Pores or bubbles inside or on the surface of products, reducing density and strength, possibly due to excessive gas content in raw materials, defects in the pressing process, or inappropriate sintering furnace parameters.
- Uneven Microstructure: Presence of laminar or porous regions in products, resulting in uneven microstructure, possibly due to uneven reaction temperatures, insufficient or excessive reaction times, or inappropriate pressing parameters.
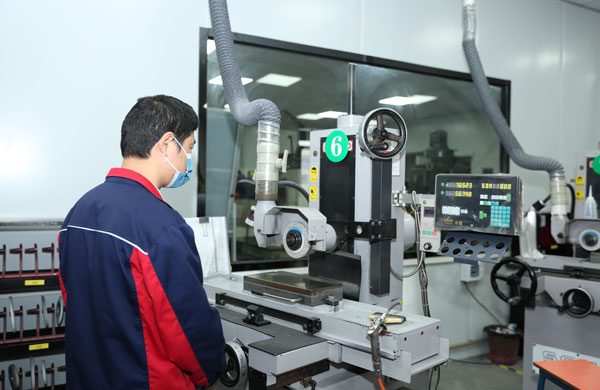
II. Comprehensive Strategies to Reduce Defects in Tungsten Carbide
To address the aforementioned defects and their causes, the following strategies can be implemented to effectively reduce the occurrence of defects:
- Material Selection and Quality Control: Select high-quality raw materials, strictly control impurity content, and strengthen quality inspection to ensure raw materials meet production standards.
- Optimization of Production Processes: Tailor appropriate process parameters such as pressing force, sintering temperature, and holding time according to product characteristics. Strengthen process control to ensure stability and consistency of parameters.
- Equipment Maintenance and Upgrading: Regularly maintain production equipment to ensure its normal operation. Keep abreast of new technologies and equipment developments, and update in a timely manner to improve production efficiency and product quality.
- Employee Training Enhancement: Strengthen technical training and quality awareness education for employees, improving their technical skills. Ensure employees are proficient in production processes and operational norms, reducing the impact of human factors on product quality.
- Strict Quality Inspection: Establish a sound quality inspection system, conduct strict inspections of various stages of production. Promptly analyze and address defective products, identify causes, and take corresponding measures for improvement.
- Introduction of Advanced Technologies: Actively introduce advanced technologies such as electrolytic grinding processing and high-precision measurement techniques to improve the production precision and product quality of tungsten carbide.
In summary, reducing defects in tungsten carbide requires comprehensive consideration of multiple aspects, including material selection, production processes, equipment, employees, quality inspection, and the introduction of advanced technologies. Only through a holistic approach can defects be effectively reduced, thereby enhancing product quality and competitiveness.