Unveiling the Key Factors Affecting the Lifespan of Tungsten Carbide Bushings
The lifespan of Tungsten Carbide bushings, a seemingly straightforward issue, actually encompasses a wealth of technical intricacies. Among the numerous influencing factors, it is crucial not only to delve into […]
The lifespan of Tungsten Carbide bushings, a seemingly straightforward issue, actually encompasses a wealth of technical intricacies. Among the numerous influencing factors, it is crucial not only to delve into the mechanisms of Tungsten Carbide bushing damage but also to pay attention to the subtle differences in processing techniques.
In the complex environment of moving parts, long-term friction is the primary culprit leading to component wear. When the clearance between the shaft and the hole gradually widens due to wear, replacement of parts becomes inevitable. To effectively extend service life and reduce replacement costs, designers ingeniously choose Tungsten Carbide, with its moderate hardness and excellent wear resistance, as the bushing material. This significantly mitigates wear issues on the shaft and seat.
Our factory business: carbide parts, mold parts, medical injection molds, precision injection molds, teflon PFA injection molding, PFA tube fittings. email: [email protected],whatsapp:+8613302615729.
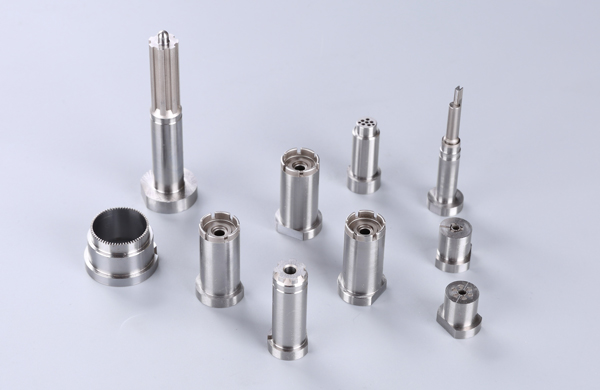
When the wear of Tungsten Carbide bushings reaches a certain level, timely replacement is a wise decision. This not only avoids the high costs associated with replacing the shaft or seat but also fully leverages the wear resistance of Tungsten Carbide bushings. During assembly, Tungsten Carbide bushings are typically used with an interference fit with the seat and a clearance fit with the shaft. Although wear cannot be completely avoided, this design maximizes the service life of Tungsten Carbide bushings.
However, some newly-trained designers hold a different view. They believe that such a setup increases manufacturing costs. However, practice is the sole criterion for testing truth. After a period of use, these equipment often still require modification according to this method during maintenance. Unfortunately, the modification process often compromises the precision of the equipment. This is because secondary processing cannot guarantee the positional accuracy of the seat hole center.
In specific operating conditions, such as those with low rotational speeds, high radial loads, and strict clearance requirements (e.g., camshafts), Tungsten Carbide bushings, with their unique advantages, become an ideal alternative to rolling bearings. To meet these requirements, Tungsten Carbide bushings must be made of materials with low hardness and high wear resistance. Additionally, their inner holes must undergo precise grinding and scraping to achieve high fitting accuracy. Furthermore, lubrication oil grooves must be provided on the inner wall to ensure adequate lubrication of the Tungsten Carbide bushings. Otherwise, in a dry grinding state, the shaft and Tungsten Carbide bushings will quickly become unusable. Therefore, during installation, it is recommended to scrape the inner wall of the Tungsten Carbide bushings to create numerous small pits, thereby enhancing lubrication. Different models of Tungsten Carbide bushings are selected based on various industrial and mining conditions.
In summary, the main factors affecting the lifespan of Tungsten Carbide bushings include pressure, speed, the product of pressure and speed, lubrication status, and load characteristics. Rotational movement and axial sliding have different requirements for Tungsten Carbide bushings, and the performance of lubricating oil also significantly impacts their lifespan. The combination of speed and pressure basically determines the lifespan of Tungsten Carbide bushings. Therefore, when selecting and using Tungsten Carbide bushings, it is essential to fully consider these factors to ensure optimal performance under harsh operating conditions.