Tungsten Carbide Welding Techniques Unveiled
Tungsten Carbide, renowned for its exceptional hardness and wear resistance, stands out in numerous industrial applications. However, this same hardness presents a challenge during processing. Consequently, in practical production, many […]
Tungsten Carbide, renowned for its exceptional hardness and wear resistance, stands out in numerous industrial applications. However, this same hardness presents a challenge during processing. Consequently, in practical production, many manufacturers opt to integrate other materials in non-critical areas through welding. This strategy not only controls the cost of Tungsten Carbide effectively but also reduces processing difficulty, achieving a dual optimization of efficiency and economy.
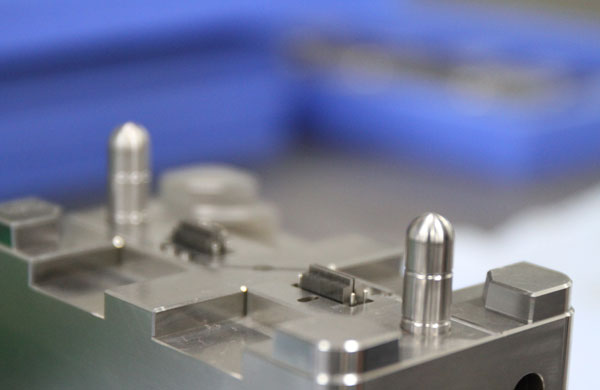
When welding Tungsten Carbide, the following key points cannot be overlooked:
Our factory business: carbide parts, mold parts, medical injection molds, precision injection molds, teflon PFA injection molding, PFA tube fittings. email: [email protected],whatsapp:+8613302615729.
- Precise Temperature Control to Prevent Cracks: Tungsten Carbide, a product of powder metallurgy forming and sintering, possesses inherent high hardness, which implies sensitivity to high temperatures. During welding, direct high-temperature burning on the Tungsten Carbide surface can easily cause cracking. Therefore, careful control of the heat source is essential to avoid direct application to the Tungsten Carbide body.
- Selection of Welding Material for Gentle Heating: Considering Tungsten Carbide’s tolerance limits to high temperatures, silver soldering becomes a wise choice. Silver’s low melting point characteristic effectively reduces the temperature requirement during welding, thereby mitigating thermal stress on Tungsten Carbide and ensuring welding quality.
- Insulation Measures to Prevent Cold Cracking: In cold environments, welded Tungsten Carbide products require special protection. Using lime for insulation is an effective means to prevent Tungsten Carbide from cracking due to sudden temperature changes (from high to low). This detail is particularly crucial during winter or in low-temperature working environments.
- Flux Assistance for Enhanced Bonding: To ensure the firmness of Tungsten Carbide welding, pre-applying flux is an indispensable step. Flux not only improves the fluidity of the solder but also effectively removes impurities from the welding surface, laying a solid foundation for the perfect fusion of Tungsten Carbide with other materials.
In summary, mastering correct welding techniques not only maximizes the performance advantages of Tungsten Carbide but also effectively avoids potential risks during processing, safeguarding your product quality and production efficiency.