Tungsten Carbide Punch Maintenance Tips: Ensuring Efficiency and Longevity
Tungsten Carbide punches play an indispensable role in the vast realm of industrial production. Mounted precisely on punching molds, they execute continuous cutting, punching, and breaking actions, transforming raw materials […]
Tungsten Carbide punches play an indispensable role in the vast realm of industrial production. Mounted precisely on punching molds, they execute continuous cutting, punching, and breaking actions, transforming raw materials into desired finished or semi-finished products through separation or plastic deformation. Yet, like all tools, even the finest Tungsten Carbide punches will not endure if not cherished and maintained. Therefore, mastering the correct usage and maintenance of Tungsten Carbide punches is crucial for enhancing production efficiency and extending tool lifespan.
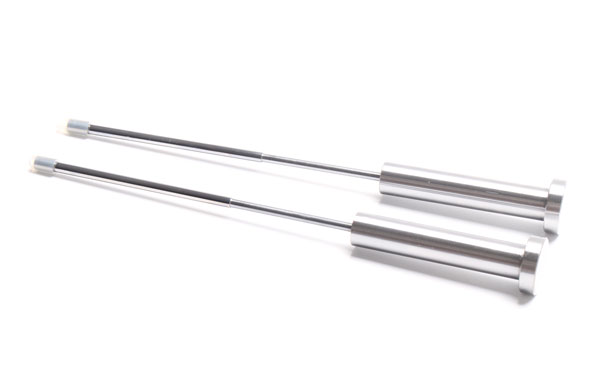
I. Tungsten Carbide Punch Installation Guide: Details Make the Difference
When installing the upper die sleeve of a Tungsten Carbide punch, every step requires caution:
Our factory business: carbide parts, mold parts, medical injection molds, precision injection molds, teflon PFA injection molding, PFA tube fittings. email: [email protected],whatsapp:+8613302615729.
- Preparation is Key: The first step is to thoroughly clean the punch and apply an appropriate amount of lubricating oil to its long shank, reducing friction and ensuring smooth operation.
- Gentle Handling, Avoid Force: Gently insert the punch into the bottom of the upper die sleeve on the large work station mold, remembering not to apply excessive force or use tools such as nylon hammers. The correct approach is to tighten the bolts on the upper die sleeve only after the punch is accurately positioned, ensuring its stability.
II. The Art of Extending Lifespan: Precise Adjustment, Detail Matters
To maximize the lifespan of Tungsten Carbide punch molds, the gap between the outer diameter of the upper die sleeve and the turret hole should be minimized as much as possible. The following steps need to be carefully executed:
- Clean and Lubricate: Thoroughly clean the keyway and inner diameter of the turret hole, and evenly apply lubricating oil, laying a solid foundation for subsequent precise installation.
- Perfect Fit, Seamless Connection: Adjust the keyway of the upper die guide bushing to ensure it perfectly matches the key of the turret hole, achieving the best positioning effect.
- Straight Insertion, No Deviation: Steadily insert the upper die sleeve guide straight into the turret hole, maintaining perpendicularity and allowing it to slide into place naturally under its own weight, avoiding any deviation.
- Gentle Correction, Ensure Precision: If the upper die sleeve deviates, use soft tools such as nylon hammers to gently tap and correct it. Repeat this process until it slides into the correct position under its own weight. Throughout this process, it is essential to note that force should be applied to the top of the punch, not to the outer diameter or top of the upper die sleeve, to prevent damage to the turret hole and affect the lifespan of individual work stations.
Finally, a friendly reminder from the Yize Mould: Correct operation methods are key to protecting Tungsten Carbide punches and extending their lifespan. Let us approach this industrial art with care and professionalism, ensuring that every punch is precise and efficient, combining both efficiency and longevity.