Tungsten Carbide: A Shining Star in Multiple Fields
I. Introduction Tungsten carbide, a hard alloy material known for its high hardness and wear resistance, has garnered widespread attention since its inception due to its unique physical and chemical […]
I. Introduction
Tungsten carbide, a hard alloy material known for its high hardness and wear resistance, has garnered widespread attention since its inception due to its unique physical and chemical properties. It has demonstrated indispensable application value in various fields such as metal processing, mold manufacturing, aerospace, oil drilling, medical equipment, and more. This article will comprehensively analyze the diverse uses of tungsten carbide, providing readers with an in-depth understanding of this remarkable material.
Our factory business: carbide parts, mold parts, medical injection molds, precision injection molds, teflon PFA injection molding, PFA tube fittings. email: [email protected],whatsapp:+8613302615729.
II. A Shining Star in Metal Processing
In the metal processing industry, tungsten carbide is undoubtedly a shining star. As the preferred material for cutting tools, tungsten carbide has won the favor of numerous manufacturers thanks to its exceptional hardness, wear resistance, and thermal stability. Whether it’s turning, milling, drilling, or grinding, tungsten carbide tools can maintain sharpness for extended periods, significantly reducing tool replacement frequency and greatly improving processing efficiency. At the same time, they can withstand extremely high cutting temperatures and pressures, ensuring stable and safe processing.
Furthermore, tungsten carbide plays a crucial role in metal forming processes such as stamping and forging. As a mold material, tungsten carbide can withstand enormous impact and frictional forces, maintaining the precise shape and high accuracy of the mold. Additionally, tungsten carbide is widely used in the manufacture of auxiliary tools such as metal cutting bands and grinding tools, further enhancing the overall efficiency and quality of metal processing.
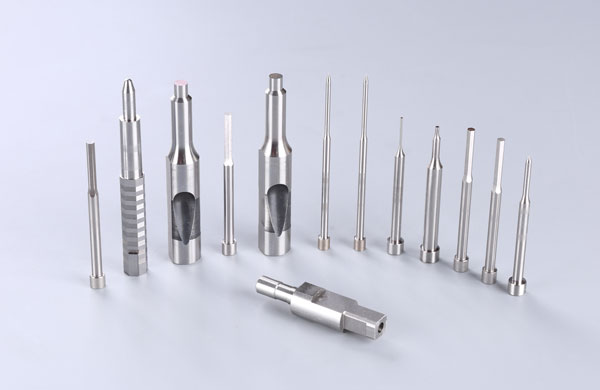
III. A Valuable Assistant in Mold Manufacturing
In the field of mold manufacturing, tungsten carbide similarly serves as a valuable assistant. With its high hardness, wear resistance, and toughness, tungsten carbide molds can maintain stable performance in high-temperature, high-pressure, and complex working environments. Therefore, they are widely used in the molding of plastics, rubbers, metals, and other materials. Not only do they ensure product precision and surface quality, but they also significantly improve production efficiency and reduce production costs.
In addition to the molds themselves, tungsten carbide plays an important role in the manufacture of mold components and auxiliary tools. For example, tungsten carbide mold ejector pins and guide posts can enhance the precision and stability of the mold; while tungsten carbide cutting knives and grinding tools can further improve the efficiency and quality of mold processing.
IV. The Ideal Choice for Aerospace
The aerospace industry imposes extremely stringent requirements on materials, and tungsten carbide has become the ideal choice due to its unique performance advantages. In the manufacture of aerospace vehicles, tungsten carbide is widely used in the production of critical components such as engine blades, turbine disks, and combustion chambers. These components need to withstand extreme working environments such as high temperatures, high pressures, and high-speed rotation, and tungsten carbide’s high hardness, thermal stability, and wear resistance are ideal for meeting these requirements.
Furthermore, tungsten carbide is used in the manufacture of other aerospace components such as landing gear and cabin doors. These components require high strength, toughness, and good corrosion resistance, and tungsten carbide possesses these characteristics.
V. A Solid Backbone in Oil Drilling
In the high-risk, high-investment field of oil drilling, tungsten carbide serves as a solid backbone. As the preferred material for drilling tools, tungsten carbide drill bits can maintain sharpness for extended periods, significantly reducing bit replacement frequency and improving drilling efficiency. At the same time, they can withstand high temperatures, high pressures, and complex geological environments, ensuring the safety and stability of the drilling process.
In addition to drill bits, tungsten carbide has other widespread applications in the oil drilling industry. For example, tungsten carbide drill pipes can withstand enormous tensile forces and torque, ensuring the smooth progress of the drilling process; while tungsten carbide reamers can enlarge the wellbore diameter, increasing oil production.
VI. The Trusted Choice in Medical Equipment
With the continuous development of medical technology, the requirements for medical equipment are becoming increasingly stringent. Tungsten carbide, with its high hardness, wear resistance, and good biocompatibility, has become the trusted choice in the medical equipment field. In dentistry, tungsten carbide drill bits are widely used in tooth restoration and implant surgeries, ensuring the precision and effectiveness of the procedures. In surgical operations, tungsten carbide surgical knives and scissors can maintain sharpness for extended periods, reducing surgery time and patient discomfort.
Furthermore, tungsten carbide is used in the manufacture of medical equipment components and auxiliary tools. For example, tungsten carbide screws and clamps can ensure the stability and precision of medical equipment; while tungsten carbide grinding tools can be used for the maintenance and upkeep of medical equipment.
VII. Widespread Applications Across Fields
In addition to the aforementioned fields, tungsten carbide has demonstrated its widespread application value in electronics, precision instruments, mining, and more. In the electronics industry, tungsten carbide is used in the manufacture of high-precision electrodes and cutting tools; in the precision instrument field, it is used to produce high-precision measurement tools and clamps; and in the mining industry, tungsten carbide is used to manufacture mining equipment and tools.
VIII. Conclusion
In summary, tungsten carbide, as a high-performance hard alloy material, has demonstrated its indispensable application value in multiple fields. With the continuous advancement of technology and the sustained development of industry, the application fields of tungsten carbide will continue to expand. We have reason to believe that in future development, tungsten carbide will play an important role in more fields, making greater contributions to the progress and development of human society.
Related Posts
- Which Tungsten Carbide Plate is Good? A Comprehensive Guide and Selection Tips
- Tungsten Carbide with Non-Magnetic Properties: Characteristics, Processing, Applications, and Future Development
- Tungsten Carbide Procurement: Ensuring Authenticity is Crucial
- A Comprehensive Exploration of Tungsten Carbide