The Art of Wire-Cutting for Precision Tungsten Carbide Products
In this era of rapid technological advancement and rising labor costs, many industries are actively embracing automation, striving to compensate for the limitations of traditional craftsmanship with high-precision equipment. In […]
In this era of rapid technological advancement and rising labor costs, many industries are actively embracing automation, striving to compensate for the limitations of traditional craftsmanship with high-precision equipment. In the field of tungsten steel products, especially those pursuing extreme precision, slow-moving wire-cutting technology has become the mainstream choice, not only enhancing production efficiency but also showcasing craftsmanship in every detail.
When it comes to the wire-cutting process for round tungsten carbide products with high requirements for both smoothness and precision, we tend to adopt the “cut one, repair three” method or the more advanced no-cut processing method. This delicate operation can effectively avoid the retention of wire marks, making the finished product surface as smooth as a mirror, fully displaying the beauty of craftsmanship.
Our factory business: carbide parts, mold parts, medical injection molds, precision injection molds, teflon PFA injection molding, PFA tube fittings. email: [email protected],whatsapp:+8613302615729.
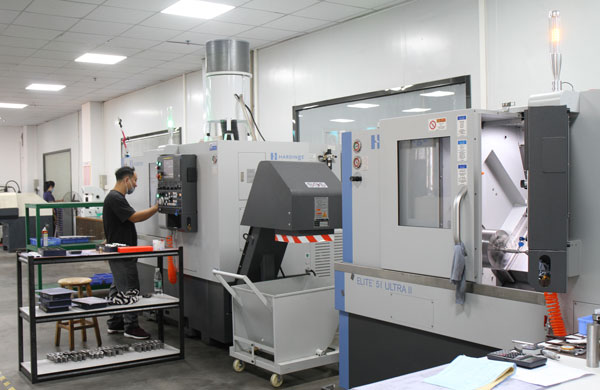
For the internal hole processing of irregular tungsten carbide products, strategy is particularly crucial. It is recommended to skillfully start cutting at the corner. This subtle adjustment, even without no-cut processing, can cleverly hide the wire head traces. Although the wire heads are actually still there, they are hardly noticeable to the naked eye, thus making the product smoothness appear higher in the eyes of customers, and satisfaction naturally increases.
The choice of the starting cutting position is also crucial for the wire cutting of irregular tungsten carbide shapes. It should be reserved on a flat area and deliberately leave raised wire heads. After the repair cutting process is completed, a grinding machine is used for fine polishing to eliminate the wire heads. This not only ensures the accuracy of the product dimensions but also preserves the flawless appearance of the product, achieving a perfect fusion of functionality and aesthetics.
In summary, mastering and applying these wire cutting techniques can not only maximize the potential of advanced equipment but also reflect the extreme pursuit of product quality and details, allowing our tungsten steel products to stand out in the market competition and win the favor of more customers.