Surface Treatment of Tungsten Carbide: Key to Enhancing Performance and Prolonging Lifespan
Tungsten carbide, a premium material known for its high hardness, strength, and melting point, is widely used in cutting tools, molds, and precision parts. However, even this exceptional material faces […]
Tungsten carbide, a premium material known for its high hardness, strength, and melting point, is widely used in cutting tools, molds, and precision parts. However, even this exceptional material faces challenges such as oxidation, corrosion, and wear. These issues not only affect its appearance but also directly shorten its lifespan and performance. Therefore, surface treatment of tungsten carbide is particularly important.
The surface treatment of tungsten carbide mainly includes the following methods, each with its unique advantages and applicable scenarios:
Our factory business: carbide parts, mold parts, medical injection molds, precision injection molds, teflon PFA injection molding, PFA tube fittings. email: [email protected],whatsapp:+8613302615729.
1. Sandblasting Treatment
Sandblasting is a common method for tungsten carbide surface treatment. By using high-pressure air or water jet, it effectively removes dirt and oxide layers from the surface, while increasing surface roughness to enhance adhesion and tightness, thereby enhancing its lifespan and strength.
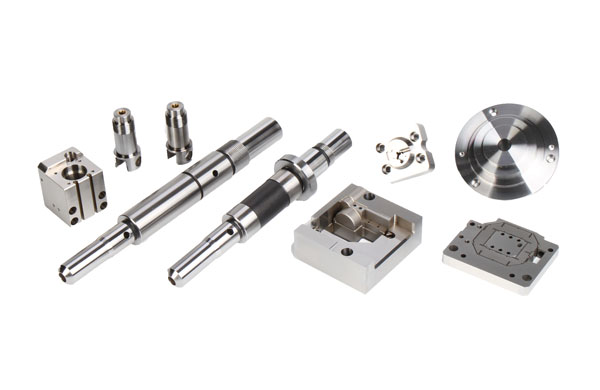
2. Electric Spark Treatment
Electric spark treatment utilizes high-frequency voltage and current to create microscopic discharge holes on the tungsten carbide surface, removing undesirable textures and oxide layers and making the surface smoother. This method significantly improves the corrosion resistance, fatigue resistance, and wear resistance of tungsten carbide.
3. Polishing Treatment
Polishing treatment involves cutting and smoothing the tungsten carbide surface using abrasives and polishing machines to remove burrs and protrusions, enhancing gloss and flatness. The polished tungsten carbide surface becomes smoother and more uniform, further improving its fatigue resistance and corrosion resistance. In recent years, new technologies such as ultrasonic polishing and electrolytic polishing have been developed for tungsten carbide with extremely high hardness to achieve more precise and efficient polishing effects.
4. Coating Treatment
Coating treatment involves covering the tungsten carbide surface with a special coating or material, such as electroplating or hot dipping. This method enhances the corrosion resistance, wear resistance, high-temperature resistance, and chemical resistance of tungsten carbide. Depending on specific usage requirements, suitable coating materials can be selected to significantly improve the lifespan and durability of tungsten carbide.
In summary, surface treatment of tungsten carbide is a crucial step in enhancing its performance and prolonging its lifespan. Each method, whether sandblasting, electric spark treatment, polishing, or coating, has its unique advantages. Choosing the appropriate surface treatment technology will ensure that tungsten carbide products achieve efficient, precise, and stable performance.