Selecting Tungsten Carbide for Mold Applications
It is not uncommon for customers to inquire, upon first contact, “What is the hardness of your Tungsten Carbide? Do you have anything harder?” However, there exists a common misconception […]
It is not uncommon for customers to inquire, upon first contact, “What is the hardness of your Tungsten Carbide? Do you have anything harder?”
However, there exists a common misconception when it comes to selecting Tungsten Carbide: that harder is always better. Hardness is determined by the content of tungsten carbide; simply put, the higher the tungsten carbide content, the greater the hardness. But it is important to note that hardness and bending strength (or toughness) are inversely proportional.
Our factory business: carbide parts, mold parts, medical injection molds, precision injection molds, teflon PFA injection molding, PFA tube fittings. email: [email protected],whatsapp:+8613302615729.
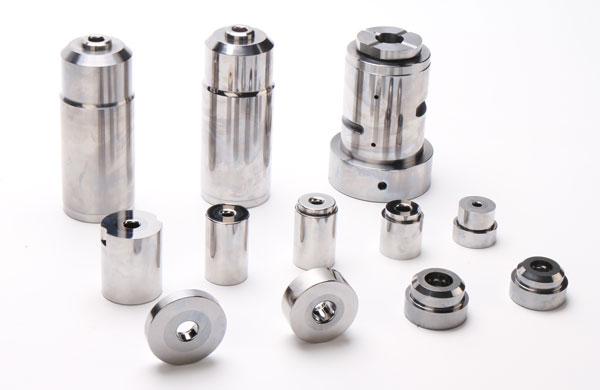
For instance, when manufacturing wear-resistant parts, it is naturally preferable to choose Tungsten Carbide with higher hardness. However, when fabricating punches for stamping products with inherently high hardness, a direct collision of hardness can often lead to damage. In such cases, Tungsten Carbide punches are prone to chipping. Conversely, opting for slightly softer Tungsten Carbide, although slightly less wear-resistant, ensures that the product is not directly damaged, while also reducing costs.
Therefore, Tungsten Carbide is not necessarily better when harder; what is crucial is selecting the most suitable material.