Precision Shaping of Tungsten Carbide: The Art of EDM Machining
Traditional turning and milling processes often prove inadequate when dealing with Tungsten Carbide, a material renowned for its exceptional hardness, particularly when shaping complex irregular pieces or those with countersunk […]
Traditional turning and milling processes often prove inadequate when dealing with Tungsten Carbide, a material renowned for its exceptional hardness, particularly when shaping complex irregular pieces or those with countersunk heads. In such cases, Electrical Discharge Machining (EDM) emerges as an indispensable solution, leveraging its unique principle of electro-erosion to overcome the challenges posed by Tungsten Carbide processing elegantly.
EDM works on the core principle of a direct collision between positive and negative charges, akin to a microscopic “lightning battle,” precisely and efficiently breaking down unwanted Tungsten Carbide material.
Our factory business: carbide parts, mold parts, medical injection molds, precision injection molds, teflon PFA injection molding, PFA tube fittings. email: [email protected],whatsapp:+8613302615729.
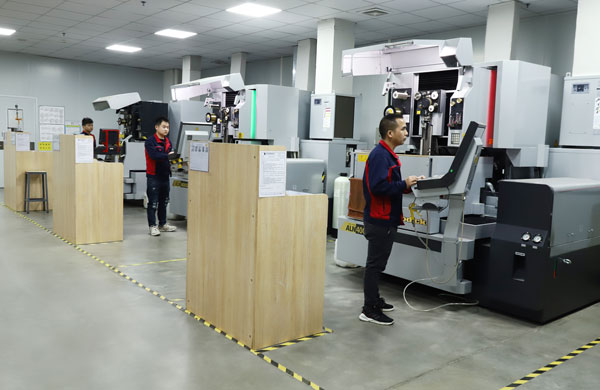
Two Major Application Scenarios in EDM of Tungsten Carbide
- Elegant Carving of Circular Workpieces
For circular workpieces, EDM demonstrates its prowess with ease. The current flows smoothly like silk, radiating uniformly in all directions from the electrode, ensuring a harmonious and balanced processing experience. Here, the key lies in perfect balancing current intensity and surface finish. While increasing the current can boost processing efficiency, it may also compromise the smoothness, leaving behind a more rugged appearance; conversely, a gentler, lower current can sculpt a finer, smoother surface. - The Delicate Challenge of Irregular Workpieces
When EDM encounters Tungsten Carbide irregular workpieces, the challenge intensifies. Although the current still emits 360 degrees from the electrode’s center, the irregular shape can lead to uneven current distribution, with some areas experiencing excessive current and others too little. In regions with overly intense currents, unsightly pitting may occur, a result of the instantaneous high-intensity current causing localized erosion of the Tungsten Carbide. To mitigate this issue, advanced EDM machines equipped with frequency vibration heads are introduced. These machines, like skilled dancers, subtly vibrate during processing intervals, effectively alleviating the problem of uneven current distribution and enhancing the overall processing effect.
In summary, EDM is not only a powerful tool in the realm of Tungsten Carbide processing but also an embodiment of the pursuit of precision and aesthetics. With the aid of technology, even the hardest materials can be transformed into works of art under our skilled hands.