Key Considerations for Grinding Tungsten Carbide Mold Accessories
In the field of mold manufacturing, tungsten carbide, with its high hardness, excellent wear resistance, and outstanding impact resistance, is widely used as a high – performance cemented carbide material. […]
In the field of mold manufacturing, tungsten carbide, with its high hardness, excellent wear resistance, and outstanding impact resistance, is widely used as a high – performance cemented carbide material. However, due to its unique physical and chemical properties, there are many matters that need special attention when grinding tungsten carbide mold accessories to ensure the grinding effect and the integrity of the mold accessories. Below, we will discuss the relevant considerations in detail.
I. Before Grinding: Careful Preparation is the Foundation
(1) Inspection of Grinding Equipment
Before grinding tungsten carbide mold accessories, it is essential to conduct a comprehensive “check – up” on the grinding equipment. Ensure that the equipment is in good working condition and free from faults and hidden dangers. In particular, carefully inspect consumable parts such as grinding wheels and grinding fluids to ensure they meet the grinding requirements.
Our factory business: carbide parts, mold parts, medical injection molds, precision injection molds, teflon PFA injection molding, PFA tube fittings. email: [email protected],whatsapp:+8613302615729.
(2) Cleaning of Mold Accessories
Before grinding, a thorough cleaning of the tungsten carbide mold accessories is required. Use organic solvents such as alcohol or acetone, or professional cleaning agents to remove impurities like oil stains and dust on the surface. Proper cleaning can prevent impurities from interfering with the grinding process and ensure the quality of the accessories.
(3) Setting of Grinding Parameters
Set appropriate grinding parameters according to the material, shape, and grinding requirements of the tungsten carbide mold accessories. These parameters include grinding speed, grinding pressure, and grinding fluid concentration. Proper grinding parameters can improve grinding efficiency and reduce wear and deformation of the mold accessories.
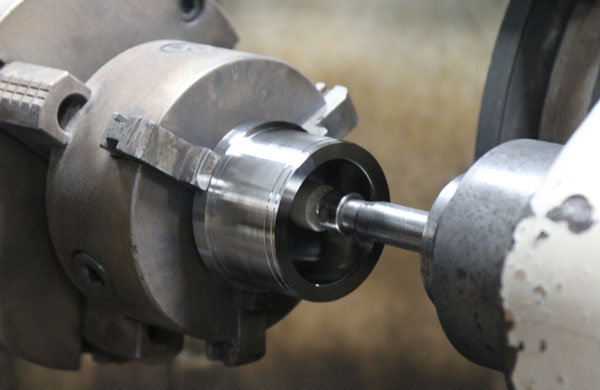
II. During Grinding: Precise Control is the Key
(1) Control of Grinding Speed
During the grinding process, strictly control the grinding speed. Excessive grinding speed may cause the surface of the mold accessories to overheat, leading to oxidation and wear. Moreover, it can also accelerate the wear of the grinding wheel and reduce grinding efficiency. Therefore, select an appropriate grinding speed based on the actual situation.
(2) Adjustment of Grinding Pressure
Grinding pressure is a crucial factor affecting the grinding effect. Excessive grinding pressure may cause cracks and deformation on the surface of the mold accessories, affecting the precision and service life of the mold. On the other hand, insufficient grinding pressure may not achieve the desired grinding effect. Therefore, adjust the grinding pressure according to the material and shape of the mold accessories.
(3) Use of Grinding Fluid
The grinding fluid plays a role in lubrication, cooling, and cleaning during the grinding process. Choosing the right grinding fluid is crucial for improving the grinding effect and the quality of the mold accessories. Select the appropriate grinding fluid based on the material and grinding requirements of the mold accessories. At the same time, ensure that the concentration and temperature of the grinding fluid are suitable to avoid adverse effects on the grinding effect caused by too high or too low concentration and temperature.
(4) Selection of Grinding Wheel
The grinding wheel is a key tool in the grinding process. Select the appropriate grinding wheel according to the material, shape, and grinding requirements of the mold accessories. Factors such as the grain size, hardness, and binder of the grinding wheel can all affect the grinding effect. Therefore, fully consider these factors when choosing a grinding wheel to ensure a good match between the grinding wheel and the mold accessories.
(5) Temperature Control
During the grinding process, closely monitor the temperature of the mold accessories and the grinding fluid. Excessive temperature may cause thermal stress cracks and deformation on the surface of the mold accessories. Therefore, take appropriate measures to reduce the temperature, such as increasing the flow rate of cooling water or reducing the grinding speed.
(6) Inspection of Grinding Quality
Regularly inspect the grinding quality of the mold accessories during the grinding process. Use tools such as magnifying glasses or microscopes to observe the surface and ensure that the grinding effect meets the requirements. If quality problems are found, promptly adjust the grinding parameters or replace tools such as the grinding wheel to ensure the grinding quality.
III. After Grinding: Proper Handling Ensures Quality
(1) Cleaning and Drying
After grinding, thoroughly clean and dry the mold accessories. Use clean water or solvents such as alcohol to remove the grinding fluid and impurities on the surface to avoid adverse effects on subsequent processing and use. Then, dry the accessories with a clean cloth or a drying machine.
(2) Rust – Proof Treatment
Tungsten carbide mold accessories are prone to rust during storage and transportation. Therefore, after grinding, conduct rust – proof treatment. Use rust – proof oil, rust – proof paper, and other tools to package and protect the mold accessories to prevent them from rusting and being damaged.
(3) Quality Recording and Traceability
Record and trace the quality of the ground mold accessories. Record information such as grinding parameters, grinding time, and grinding personnel. This helps in tracing and dealing with problems that may occur during subsequent processing and use. At the same time, it can also provide references for future grinding work.
IV. Conclusion
Grinding tungsten carbide mold accessories is a complex and delicate task. During the grinding process, it is necessary to strictly control parameters such as grinding speed, grinding pressure, and the use of grinding fluid, and choose the appropriate grinding wheel and grinding fluid to ensure the grinding effect and the quality of the mold accessories. At the same time, sufficient preparation before grinding and proper post – grinding handling are also essential to ensure the integrity and service life of the mold accessories. By strictly following these considerations and measures, the grinding efficiency and quality of tungsten carbide mold accessories can be improved, contributing to the development of the mold manufacturing industry.