Introduction to Tungsten Carbide Parts
Tungsten carbide parts, as key components in modern industry, are widely favored for their high hardness, wear resistance, and thermal stability. Tungsten carbide, made from tungsten carbide (WC) and cobalt […]
Tungsten carbide parts, as key components in modern industry, are widely favored for their high hardness, wear resistance, and thermal stability. Tungsten carbide, made from tungsten carbide (WC) and cobalt (Co) or other metal binders through powder metallurgy, has a hardness second only to diamond. Tungsten carbide parts not only inherit these advantages but also exhibit good chemical stability and machinability.
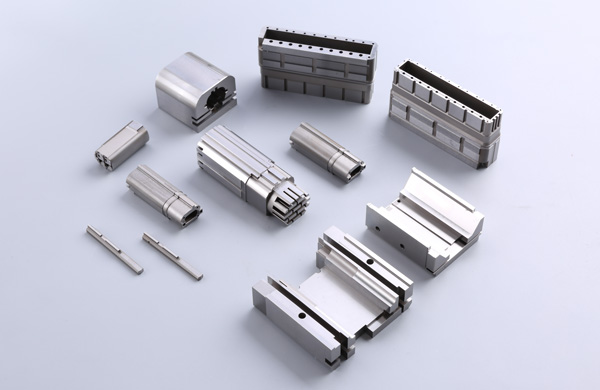
In terms of manufacturing process, tungsten carbide parts undergo multiple steps including material selection, mixing and pressing, sintering, subsequent processing, and quality inspection to ensure performance standards are met. They play crucial roles in various fields such as mechanical manufacturing, mold making, petrochemicals, aerospace, and more. For instance, cutting tools and transmission components in mechanical manufacturing, high-temperature and high-pressure molds in mold making, and critical engine components in aerospace all rely on tungsten carbide parts.
Our factory business: carbide parts, mold parts, medical injection molds, precision injection molds, teflon PFA injection molding, PFA tube fittings. email: [email protected],whatsapp:+8613302615729.
When purchasing tungsten carbide parts, it is important to select the appropriate type and specification based on actual needs and buy from reputable sources. During use, proper maintenance and timely replacement of worn parts are essential to ensure equipment operates smoothly and safely.
In summary, tungsten carbide parts, with their excellent properties and wide range of applications, have become an indispensable part of modern industry, and their future development prospects are promising.