Interpretation of Common Tungsten Carbide Codes
In the grand arena of industrial manufacturing, tungsten carbide shines like a brilliant star, playing a crucial role with its unique physical and chemical properties. As a high – performance […]
In the grand arena of industrial manufacturing, tungsten carbide shines like a brilliant star, playing a crucial role with its unique physical and chemical properties. As a high – performance cemented carbide material, different codes of tungsten carbide hide varying compositions, properties, and applications. Next, let’s delve into the mysteries of common tungsten carbide codes together.
I. Overview of the Tungsten Carbide Code System
The tungsten carbide code system is like a set of precise codes, cleverly combined with letters and numbers. These codes not only serve as identifiers for tungsten carbide but also reflect its main components, performance characteristics, and applicable scenarios. Below, we will provide a detailed interpretation of some common tungsten carbide codes.
Our factory business: carbide parts, mold parts, medical injection molds, precision injection molds, teflon PFA injection molding, PFA tube fittings. email: [email protected],whatsapp:+8613302615729.
II. Detailed Explanation of Common Tungsten Carbide Codes
- YG Series
- The YG series is the national standard code for tungsten carbide. The letter “Y” represents cemented carbide, and “G” is taken from the initial letter of the English abbreviation for cemented carbide (Tungsten Carbide – Cobalt Alloy). This series is further subdivided based on different numbers, such as YG3, YG6, YG8, YG15, etc. These numbers usually represent the cobalt content. For example, the “6” in YG6 indicates that the cobalt content is about 6%. Cobalt, as a key element in tungsten carbide, can significantly improve its toughness and impact resistance.
- YG6: As a commonly used tungsten carbide material, the cobalt content is about 6%. It has relatively high hardness and wear resistance, with a heat – treatment hardness range of 90 – 94HRA, which falls into the medium – hardness category. It is suitable for manufacturing drills and cutting tools.
- YG15: Compared with YG6, YG15 has a lower cobalt content of about 15%. Although its hardness is slightly lower (about 85HRA), it has good strength and impact resistance, making it suitable for manufacturing cutting tools that need to withstand a certain amount of impact force.
- W Series
- The W – series tungsten carbide codes start with the letter “W”, and the subsequent numbers usually represent the main components or special properties of the tungsten carbide.
- W1: The most basic type of tungsten carbide, with a pure tungsten content of over 99.5%. Due to its high melting point and high hardness, it is suitable for making high – temperature parts and electronic devices.
- W2: Tungsten carbide containing molybdenum, which has excellent high – temperature strength and toughness. W2 tungsten carbide is often used to make components in high – temperature environments, such as circuit breaker contacts and high – temperature furnaces.
- W5, W15, W18: These codes represent tungsten carbide containing cobalt, with the cobalt content gradually increasing. They have relatively high hardness and corrosion resistance and are suitable for manufacturing cutting tools and knives. In particular, W18 tungsten carbide, due to its high cobalt content, has good grindability and wear resistance, making it suitable for making high – quality cutting tools.
- Special Codes
In addition to the common YG and W series, there are also some tungsten carbide materials with special codes, such as YG20 and YG20C. These materials are optimized and improved based on the YG series to meet more special processing requirements.- YG20: A low – hardness alloy material but with good wear resistance and high – temperature strength. YG20 tungsten carbide is often used to manufacture brazing tools, forging dies, and petroleum machinery parts.
- YG20C: Further optimized based on YG20, with a hardness of 85HRA and a bending strength of 2500MPa. YG20C tungsten carbide is suitable for making standard parts, bearings, and cold – heading and cold – stamping dies for tungsten carbide.
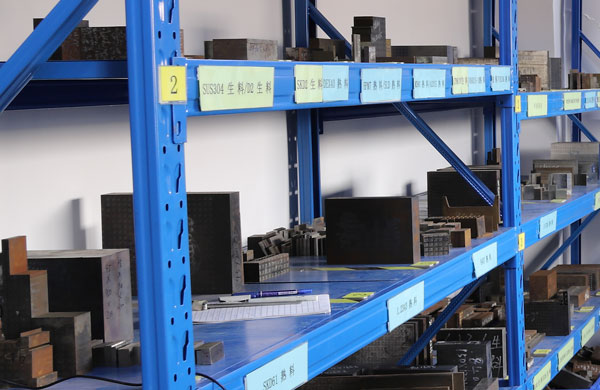
III. Key Points for the Selection and Application of Tungsten Carbide Codes
In practical applications, selecting the appropriate tungsten carbide code is extremely crucial. Different codes imply different compositions, properties, and applications, so they must be chosen according to specific processing requirements and environmental conditions. For example, when manufacturing cutting tools, tungsten carbide materials with high hardness and wear resistance need to be selected; when manufacturing components in high – temperature environments, tungsten carbide materials with good high – temperature strength and toughness should be chosen.
In addition, the tungsten carbide code is closely related to its manufacturing process and cost. Different codes represent different production processes and raw material ratios, so the manufacturing costs will also vary. When selecting a tungsten carbide code, factors such as performance, application, and cost need to be comprehensively considered to achieve the best cost – performance ratio.
IV. Conclusion
Tungsten carbide, as an important material in the field of modern industrial manufacturing, plays an irreplaceable role with its excellent performance. Different tungsten carbide codes correspond to different compositions, properties, and applications. Only by making reasonable choices according to specific needs can its advantages be fully utilized. This article provides a comprehensive introduction to common tungsten carbide codes and their characteristics, hoping to help readers better understand and apply this material. With the continuous progress of technology and the continuous innovation of processes, it is believed that the performance and application fields of tungsten carbide will usher in broader development prospects.