In-depth Analysis of Tungsten Carbide Punch Sintering Process
The sintering process of tungsten carbide punch is a precise and complex procedure that skillfully transforms powder into a blank through compression, followed by heating in a sintering furnace to […]
The sintering process of tungsten carbide punch is a precise and complex procedure that skillfully transforms powder into a blank through compression, followed by heating in a sintering furnace to a specific temperature (sintering temperature) and maintaining it for a certain period (holding time), and finally cooling to obtain the desired tungsten carbide punch with required properties. This process can be divided into four core stages, each stage encapsulating the mysteries of material transformation.
1. Removal of Forming Agent and Pre-sintering Stage
Our factory business: carbide parts, mold parts, medical injection molds, precision injection molds, teflon PFA injection molding, PFA tube fittings. email: [email protected],whatsapp:+8613302615729.
This stage marks the initial formation of the sintered body. As the temperature gradually rises, the forming agent begins to decompose or vaporize, slowly exiting the stage of the sintered body. Meanwhile, this process may be accompanied by a slight carburization of the sintered body, with the degree of carburization varying depending on the type, amount, and sintering process of the forming agent. During this period, the oxides on the surface of the tungsten carbide punch powder are reduced, particularly at the sintering temperature where hydrogen can effectively reduce the oxides of cobalt and tungsten. If the forming agent is removed and sintering is carried out in a vacuum environment, the carbon-oxygen reaction is relatively mild. Additionally, the contact stress between powder particles gradually dissipates, and the bonded metal powder begins to undergo recovery and recrystallization, with surface diffusion phenomena emerging, resulting in an increase in the strength of the compressed block.
2. Solid-phase Sintering Stage (800℃-Eutectic Temperature)
In the temperature range before the appearance of the liquid phase, apart from continuing the processes that occurred in the previous stage, solid-phase reactions and diffusion intensify, plastic flow enhances, and the sintered body exhibits significant shrinkage.
3. Liquid-phase Sintering Stage (Eutectic Temperature-Sintering Temperature)
Once the sintered body enters the liquid phase, the shrinkage process is rapidly completed, followed by changes in the crystalline structure, forming the basic organization and structure of the alloy.
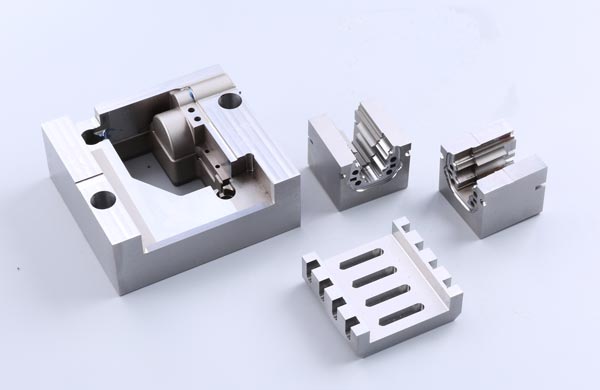
4. Cooling Stage (Sintering Temperature-Room Temperature)
During this stage, the organization and phase composition of the tungsten carbide punch change subtly according to different cooling conditions. Utilizing this characteristic, heat treatment can be applied to the tungsten carbide punch to enhance its physical and mechanical properties, which gives it a superior value for use.
In summary, the sintering process of tungsten carbide punch is a precise procedure that integrates temperature control, time management, and material phase transformation. Each step is crucial, jointly determining the final product’s quality and performance.