In-depth Analysis of Tungsten Carbide Punch Customization and Production Processing
Stamping production plays a pivotal role in the industrial sector, serving as an efficient method for mass production and a crucial process for the shaping of numerous products. Among the […]
Stamping production plays a pivotal role in the industrial sector, serving as an efficient method for mass production and a crucial process for the shaping of numerous products. Among the core components of stamping molds, punches stand out as the most vital elements, directly impacting production efficiency. Notably, Tungsten Carbide punches, representing the high-end market, have become leaders due to their exceptional performance.
Tungsten Carbide, also known as cemented carbide, is hailed as the “teeth of industry,” exhibiting unparalleled advantages in wear-resistant and impact-resistant environments. As an integral part of precision mold components, punches not only enhance the strength of ejector pins but also effectively prevent their deformation or breakage, ensuring the stable operation of molds.
Our factory business: carbide parts, mold parts, medical injection molds, precision injection molds, teflon PFA injection molding, PFA tube fittings. email: [email protected],whatsapp:+8613302615729.
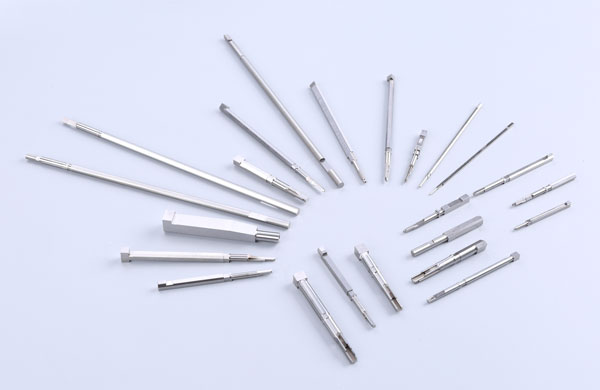
Punches, acting as connectors within molds, have a profound impact on the overall performance of the mold. Therefore, the processing requirements for punches are extremely stringent. In the mold cavity, punches undergo both movement and sliding, resulting in intense friction with the cavity surface. This necessitates punches to possess outstanding wear resistance, which is primarily determined by hardness. Generally, the higher the hardness of the punch, the lower the wear and the better the wear resistance. Furthermore, wear resistance is also closely related to the type, quantity, shape, size, and distribution of carbides in the material.
In the continuous production of stamping molds, punches, as core working components, directly influence the production efficiency of stamped products through their performance and lifespan. This is particularly true for high-end precision mold products, which demand even higher performance from punches. To meet this demand, cemented carbide punches and Tungsten Carbide punches have emerged. They are used in large quantities per application and require each punch to maintain a high degree of consistency. This necessitates strict control over every process detail during precision processing to ensure product stability and reliability.
Our company fully understands this and therefore customizes the production of cemented carbide punches and Tungsten Carbide punches in strict accordance with the drawings provided by Our clients. Our products exhibit excellent consistency, with a precision tolerance of +0.002 and a surface finish of 0.2 for punches and punch pins, achieving a mirror-like effect. Whether it is the blank processing of cemented carbide rods or the precision size processing of cemented carbide punches, we adhere to strict tolerance requirements and ensure product consistency in batch production, meeting the highest standards of our clients.
The customization and production processing of Tungsten Carbide punches involves the technical challenges of batch production and precision processing, which must be accurately completed according to the requirements of the precision mold equipment used in actual operations. Whether it is the micrometer-level precision required for production and processing or the precision size inspection after Tungsten Carbide punch processing, reliance on exquisite processing techniques and advanced processing equipment is crucial. These factors collectively constitute the key to the successful mass production of Tungsten Carbide punches.