How to Improve the Working Efficiency of Tungsten Carbide Dies?
I. Introduction In the vast stage of modern manufacturing, molds play a pivotal role, with their performance and working efficiency directly linked to product quality and production rate. Tungsten carbide […]
I. Introduction
In the vast stage of modern manufacturing, molds play a pivotal role, with their performance and working efficiency directly linked to product quality and production rate. Tungsten carbide molds, with their outstanding hardness, wear resistance, and strength characteristics, occupy a prominent position in the mold manufacturing field. However, facing the intensifying market competition and ever-increasing consumer demands, how to further tap and enhance the working efficiency of tungsten carbide molds has become a focus of attention both inside and outside the industry. This article will delve into the ways to improve the working efficiency of tungsten carbide molds from multiple dimensions, including design optimization, processing precision enhancement, usage and maintenance optimization, personnel quality improvement, and the introduction of intelligent and automation technologies, contributing wisdom to the vigorous development of the mold manufacturing industry.
Our factory business: carbide parts, mold parts, medical injection molds, precision injection molds, teflon PFA injection molding, PFA tube fittings. email: [email protected],whatsapp:+8613302615729.
II. Optimizing the Design of Tungsten Carbide Molds: Precision as the Foundation, Structure as the Soul
- Precise Calculation of Mold Dimensions: At the beginning of the design, the mold dimensions are carefully calculated to ensure a seamless fit between the mold and the product, reducing production errors and improving efficiency.
- Reasonable Selection of Mold Structure: Tailor the mold structure according to product characteristics, simplifying complexity, reducing processing difficulty, and enhancing manufacturing precision and service life.
- Introducing Advanced Design Technologies: Leverage the power of technologies such as CAD and FEA for precise design and simulation analysis, quickly identifying problems and optimizing design to enhance the efficiency and reliability of the mold.
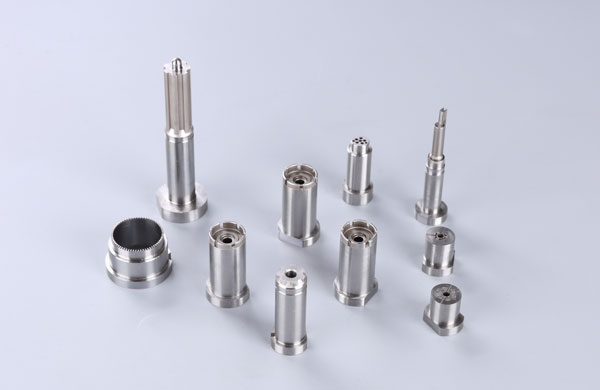
III. Improving the Processing Precision of Tungsten Carbide Molds: Equipment as the Priority, Technology as the Wings
- Selecting High-Precision Processing Equipment: Rely on high-precision equipment such as CNC milling machines and electrical discharge machining machines to ensure the processing precision and surface quality of the molds.
- Strict Control of the Processing Process: Finely regulate cutting parameters, strengthen processing quality inspection, and ensure process stability and precision.
- Adopting Advanced Processing Technologies: Laser processing, ultrasonic processing, and other cutting-edge technologies assist in high-precision mold processing, improving efficiency and service life.
IV. Optimizing the Use and Maintenance of Tungsten Carbide Molds: Conditions as the Key, Maintenance as the Foundation
- Reasonable Selection of Usage Conditions: Tailor usage conditions based on product material and process requirements to avoid mold damage.
- Strengthening Mold Lubrication and Cooling: Lubrication reduces friction, and cooling lowers temperature, working together to extend mold life.
- Regular Inspection and Maintenance: Regularly inspect molds and promptly address wear and cracks to ensure optimal mold condition and efficiency.
V. Improving the Quality of Mold Operators: Training as the Basis, Incentives as the Driving Force
- Strengthening Training and Education: Provide systematic training to enhance operators’ skills and safety awareness, reducing operational errors.
- Establishing an Incentive Mechanism: Encourage learning of new technologies, improve working efficiency and quality, and stimulate enthusiasm and creativity.
VI. Introducing Intelligent and Automation Technologies: Intelligence as the Core, Automation as the Wings
- Introducing an Intelligent Management System: Real-time monitoring and data analysis to promptly identify and address abnormalities, improving mold efficiency and reliability.
- Introducing Automated Production Lines: Combining tungsten carbide molds with automated production lines to significantly improve production efficiency, reduce costs, and enhance quality.
VII. Conclusion: Comprehensive Measures for Continuous Improvement
Improving the working efficiency of tungsten carbide molds is a systematic engineering task that requires concerted efforts from design, processing, usage and maintenance, personnel quality, to intelligent and automation technologies. Through the implementation of these measures, not only can the working efficiency and service life of molds be significantly enhanced, but product quality can also be improved, production efficiency can be increased, costs can be reduced, and corporate competitiveness can be strengthened. The mold manufacturing industry should boldly explore, actively practice, and jointly promote the continuous progress of the industry, creating a brilliant future together.