How to Choose Tungsten Carbide Rolling Wheels? A Comprehensive Guide
Introduction In the grand stage of modern industrial production, tungsten carbide rolling wheels play a pivotal role. They are like highly skilled craftsmen directly involved in the processing and manufacturing […]
Introduction
In the grand stage of modern industrial production, tungsten carbide rolling wheels play a pivotal role. They are like highly skilled craftsmen directly involved in the processing and manufacturing of various products. The quality and performance of these wheels are not only closely related to the quality of the products but also have a significant impact on production costs. However, when we enter the market, we are confronted with a dazzling array of tungsten carbide rolling wheel products, which vary in type and performance. So, how can we accurately select the most suitable tungsten carbide rolling wheel from so many options? This has become a critical issue that many enterprises urgently need to address. This article will analyze the selection methods of tungsten carbide rolling wheels in detail from multiple dimensions such as material characteristics, process requirements, and application environments, to help enterprises easily choose the ideal product.
Basic Characteristics of Tungsten Carbide Rolling Wheels
Tungsten carbide rolling wheels are mainly composed of tungsten carbide (WC) and a metal binder phase (usually cobalt, Co). This unique composition endows them with a series of remarkable characteristics: high hardness, allowing them to handle various hard materials with ease; high strength, ensuring they can withstand significant external forces without deforming or breaking; excellent wear resistance, enabling them to maintain outstanding performance over long – term use; and good corrosion resistance, allowing them to work stably in harsh chemical environments. It is precisely these outstanding characteristics that have made tungsten carbide rolling wheels widely used in many fields such as metal processing and mold manufacturing, becoming an indispensable and important tool in industrial production.
Our factory business: carbide parts, mold parts, medical injection molds, precision injection molds, teflon PFA injection molding, PFA tube fittings. email: [email protected],whatsapp:+8613302615729.
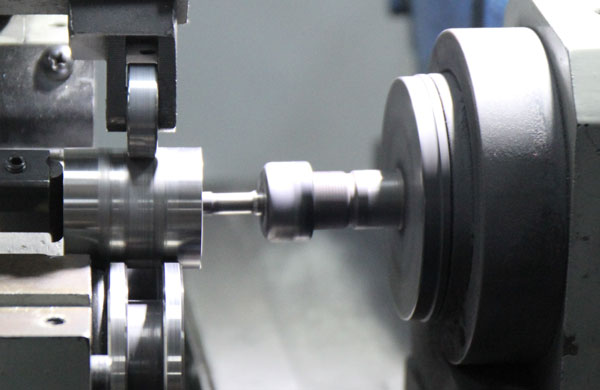
Selection Methods for Tungsten Carbide Rolling Wheels
Consideration of Material Characteristics
- Hardness: Hardness is one of the key indicators for measuring the performance of tungsten carbide rolling wheels. Generally speaking, the higher the hardness, the better the wear resistance, but the toughness will decrease accordingly. Therefore, when choosing tungsten carbide rolling wheels, we must select an appropriate hardness grade based on the hardness of the specific processing materials and processing requirements.
- Strength: Strength reflects the resistance of tungsten carbide rolling wheels when subjected to external forces. A high – strength rolling wheel is like a powerful warrior, better able to withstand the impact and extrusion during the processing, ensuring processing accuracy and efficiency. When selecting, we should pay attention to the strength parameters of the rolling wheels and choose those with sufficient strength.
- Wear Resistance: Wear resistance is one of the core performances of tungsten carbide rolling wheels. A rolling wheel with good wear resistance is like an indefatigable long – distance runner, able to maintain stable performance over long – term use, reduce replacement frequency, and lower production costs. When selecting, we can evaluate its wear resistance performance by checking the product’s wear resistance test reports.
- Corrosion Resistance: In some special working environments, such as acidic, alkaline, or other corrosive media, the corrosion resistance of the rolling wheels becomes particularly important. It is like putting on a corrosion – resistant coat for the rolling wheels, effectively preventing them from being corroded and damaged. Therefore, in these special environments, we must choose tungsten carbide rolling wheels with good corrosion resistance.
Consideration of Process Requirements
- Processing Accuracy: Processing accuracy is one of the important indicators for measuring the performance of tungsten carbide rolling wheels. It is directly related to whether the quality of the processed products meets the standards. When selecting, we should choose rolling wheels with corresponding processing accuracy based on specific processing requirements. If high processing accuracy is required, we must select products with a higher accuracy grade.
- Processing Speed: Processing speed is crucial for improving production efficiency. A rolling wheel that can adapt to a higher processing speed is like a high – speed racing car, able to quickly complete processing tasks and improve production efficiency. When selecting, we need to consider the processing speed range that the rolling wheel can adapt to and ensure it can meet production needs.
- Processing Temperature: Processing temperature has a non – negligible impact on the performance of tungsten carbide rolling wheels. In high – temperature environments, the hardness and strength of the rolling wheels will decrease, just as people tend to get tired in high temperatures. Therefore, when selecting, we should fully consider the impact of processing temperature on the performance of the rolling wheels and choose products that can maintain good performance in high – temperature environments.
Consideration of Application Environments
- Working Environment: Factors such as temperature, humidity, and corrosiveness in the working environment can significantly affect the performance of tungsten carbide rolling wheels, like invisible hands. When selecting, we need to thoroughly understand the specific working environment and choose rolling wheels with corresponding performance. For example, in high – temperature, high – humidity, or corrosive gas environments, we should choose products with good high – temperature resistance, moisture resistance, and corrosion resistance.
- Processing Materials: The processing of different materials places different requirements on tungsten carbide rolling wheels. Just as different locks require different keys, processing different materials requires selecting suitable rolling wheels. When selecting, we should carefully choose appropriate rolling wheels based on the type, hardness, toughness, and other characteristics of the processing materials.
- Equipment Matching: Tungsten carbide rolling wheels need to be perfectly matched with corresponding equipment to achieve optimal performance. Just as a good car needs to be equipped with a suitable engine, the matching degree between the rolling wheel and the equipment directly affects the processing effect and efficiency. When selecting, we should consider factors such as the model, specifications, and power of the equipment to ensure that the rolling wheel can work well with the equipment to achieve efficient and stable processing.
Summary
The selection of tungsten carbide rolling wheels is a process that requires comprehensive consideration of multiple factors. We should fully understand the basic characteristics of tungsten carbide rolling wheels and, combined with specific processing needs and application environments, carefully weigh various factors like a shrewd shopper, and choose tungsten carbide rolling wheels with appropriate hardness, strength, wear resistance, and corrosion resistance. At the same time, we should also pay attention to factors such as processing accuracy, processing speed, and processing temperature to ensure that the rolling wheels can meet production needs, improve product quality, and enhance production efficiency.
In practical applications, we cannot ignore the maintenance and upkeep of tungsten carbide rolling wheels. We should regularly inspect and replace them, just as we regularly maintain cars, to ensure they always maintain good performance. In addition, with the continuous progress of technology and the continuous optimization of processes, the performance and application fields of tungsten carbide rolling wheels will be further expanded and enhanced. We should keep up with the pace of the times, continuously learn and master new knowledge and technologies, so as to better select and use tungsten carbide rolling wheels and contribute to the development of enterprises.