How to Choose Tungsten Carbide Rolling Wheels
Introduction Tungsten carbide rolling wheels, as essential components in modern industrial production, directly impact production efficiency and product quality with their performance. With the continuous development of industrial technology, the […]
Introduction
Tungsten carbide rolling wheels, as essential components in modern industrial production, directly impact production efficiency and product quality with their performance. With the continuous development of industrial technology, the performance requirements for tungsten carbide rolling wheels are becoming increasingly stringent. This article will provide a comprehensive analysis of how to choose tungsten carbide rolling wheels, covering consideration factors, specific steps, and precautions, to help you easily master the selection process.
Key Factors to Consider When Choosing Tungsten Carbide Rolling Wheels
- Material Hardness and Wear Resistance
Tungsten carbide is renowned for its high hardness and wear resistance, so when choosing, the material hardness and wear resistance are the primary considerations. The higher the hardness, the greater the wear resistance, enabling stable performance under harsh working conditions. Depending on production needs, select tungsten carbide rolling wheels with different hardness levels. - Size Specifications
Size specifications are another important consideration when choosing tungsten carbide rolling wheels. Different production equipment requires rolling wheels of different sizes, so selection should be based on the specific specifications of the equipment. Additionally, pay attention to the tolerance range of the rolling wheels to ensure a perfect match with the equipment. - Surface Treatment
Surface treatment has a significant impact on the performance of tungsten carbide rolling wheels. Mirror polishing results in a smooth surface with high precision, suitable for products with high surface quality requirements; sandblasting increases the surface roughness, improving the rolling effect. Choose the appropriate surface treatment method based on actual needs. - Manufacturer and Brand
Choose products from reputable manufacturers and brands for better quality assurance. These manufacturers have advanced production equipment and strict quality control systems, ensuring the quality and performance of tungsten carbide rolling wheels.
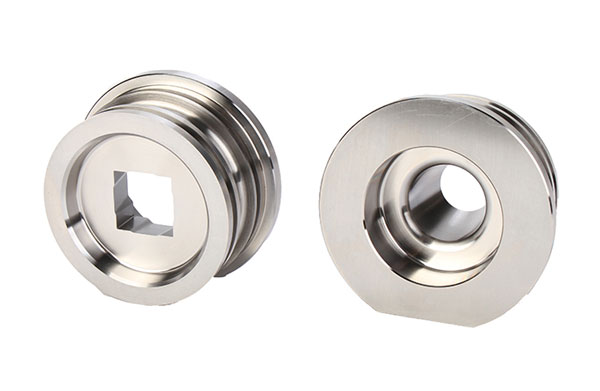
Specific Steps for Choosing Tungsten Carbide Rolling Wheels
- Clarify Needs
Before choosing, clarify your needs, including equipment requirements, product size specifications, and surface quality requirements. These needs will directly guide the selection of tungsten carbide rolling wheels. - Understand the Market
Through online searches, industry exhibitions, and other channels, learn about the product performance, prices, and other information from different brands and manufacturers, laying the foundation for comparative selection. - Comparative Selection
Based on factors such as material hardness, wear resistance, size specifications, and surface treatment, conduct a comprehensive comparison of tungsten carbide rolling wheels from different brands and manufacturers, selecting the product with the best cost-effectiveness. - Purchase and Inspection
When purchasing, sign a contract with the supplier, specifying product specifications, quantities, prices, etc. During inspection, strictly check the tungsten carbide rolling wheels to ensure they meet the contract requirements and production needs.
Points to Note When Choosing Tungsten Carbide Rolling Wheels
- Application Scope
Different models of tungsten carbide rolling wheels are suitable for different production equipment and products. When choosing, select based on actual needs to avoid poor production results or equipment damage due to improper selection. - Maintenance and Upkeep
Regularly maintain and upkeep tungsten carbide rolling wheels to extend their service life and improve performance. During use, pay attention to checking for wear and replace severely worn parts in a timely manner. - Safe Operation
Strictly follow safe operating procedures to ensure personal and equipment safety. Avoid safety accidents caused by improper operations.
Conclusion
Choosing tungsten carbide rolling wheels is a process that requires comprehensive consideration of multiple factors. It is necessary to clarify needs, understand the market, conduct comparative selection, and pay attention to issues such as application scope, maintenance and upkeep, and safe operation. Only in this way can the smooth progress of production and the stable improvement of product quality be ensured.
Our factory business: carbide parts, mold parts, medical injection molds, precision injection molds, teflon PFA injection molding, PFA tube fittings. email: [email protected],whatsapp:+8613302615729.