How to Choose Tungsten Carbide Drill Bushings
I. Introduction Tungsten carbide drill bushings, as indispensable tools in the field of mechanical processing, directly impact processing precision and efficiency in their selection. With their notable characteristics of high […]
I. Introduction
Tungsten carbide drill bushings, as indispensable tools in the field of mechanical processing, directly impact processing precision and efficiency in their selection. With their notable characteristics of high hardness, high wear resistance, and high thermal hardness, tungsten carbide drill bushings play a pivotal role in drilling operations. However, the market is flooded with a wide variety of tungsten carbide drill bushings, each with different performance attributes. How to select a suitable tungsten carbide drill bushing has become a focus of attention for many mechanical processing practitioners. This article will provide a detailed interpretation of the selection criteria, methods, and precautions for tungsten carbide drill bushings.
II. Selection Criteria for Tungsten Carbide Drill Bushings
- Compatibility Principle: The selection of tungsten carbide drill bushings should first satisfy compatibility with the drilling tools and workpieces. The size, precision, and material of the bushings need to match the drilling tools to ensure stable and reliable processing. At the same time, the bushings should also adapt to the material and hardness characteristics of the workpieces to achieve optimal processing results.
- Durability Principle: Tungsten carbide drill bushings should have a long service life to reduce the number of replacements and downtime, thereby improving processing efficiency. Durability primarily depends on the material, manufacturing process, and heat treatment process of the bushings. Therefore, attention should be paid to these aspects when making a selection.
- Economic Principle: Under the premise of satisfying compatibility and durability, tungsten carbide drill bushings with high cost-effectiveness should be chosen. Although price is not the only consideration, excessively high prices will increase production costs, while excessively low prices may indicate quality issues. Therefore, a comprehensive consideration of price and quality is necessary when making a selection.
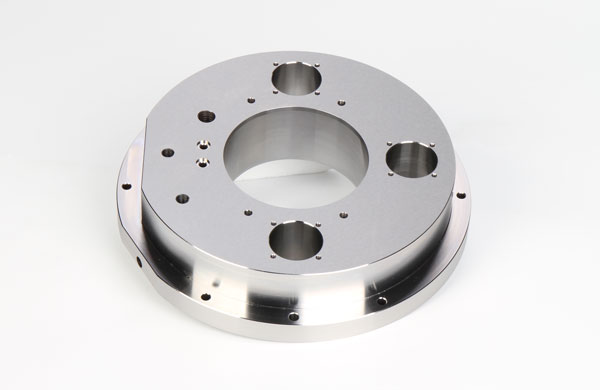
III. Methods for Selecting Tungsten Carbide Drill Bushings
- Understand Processing Requirements: Before selecting, it is necessary to clarify the material, hardness, dimensional accuracy requirements, and processing volume of the workpieces to determine the required type, size, and precision grade of the bushings.
- Choose Suitable Material: The material of tungsten carbide drill bushings is a key factor affecting their performance. High-speed steel bushings have high toughness and good wear resistance, making them suitable for general precision processing. Carbide bushings have higher hardness and better wear resistance, making them suitable for high-precision and high-hardness processing. The choice should be made based on the processing requirements.
- Determine Size and Precision Grade: Select the appropriate size and precision grade of the bushings according to the processing requirements to ensure compatibility with the drilling tools and meet the requirements of the workpieces.
- Consider Heat Treatment Process: The heat treatment process has a significant impact on the performance of tungsten carbide drill bushings. Proper heat treatment can improve the hardness, wear resistance, and thermal hardness of the bushings, extending their service life. Attention should be paid to whether the heat treatment process meets the requirements when making a selection.
- Choose Reputable Brands and Reliable Suppliers: Reputable brands and reliable suppliers usually have advanced production processes and strict quality control systems, ensuring the quality and performance of tungsten carbide drill bushings. Priority should be given to products from these brands when making a selection.
IV. Precautions for Selecting Tungsten Carbide Drill Bushings
- Avoid Blindly Pursuing Low Prices: Although price is one of the considerations, blindly pursuing low prices should be avoided. Low-priced products may have quality issues, affecting processing results and service life. A comprehensive consideration of price and quality is necessary when making a selection.
- Pay Attention to Compatibility: Ensure that the tungsten carbide drill bushings are compatible with the drilling tools and workpieces. Poor compatibility may lead to unstable and unreliable processing, affecting processing results and service life.
- Focus on Heat Treatment Process: The heat treatment process has a significant impact on the performance of tungsten carbide drill bushings. Attention should be paid to whether the heat treatment process meets the requirements when making a selection. Improper heat treatment may lead to a decrease in the performance of the bushings.
- Regular Replacement and Maintenance: Tungsten carbide drill bushings will gradually wear and damage during use, requiring regular replacement and maintenance. The wear condition of the bushings should be checked during use, and severely worn bushings should be replaced in a timely manner. Additionally, regular maintenance and cleaning of the bushings should be carried out.
V. Conclusion
The selection of tungsten carbide drill bushings is crucial for ensuring processing precision and improving processing efficiency. When making a selection, the principles of compatibility, durability, and economy should be followed, and the appropriate material, size, and precision grade should be chosen based on the processing requirements. Attention should also be paid to the heat treatment process and the choice of reputable brand products. During use, regular replacement and maintenance of the bushings are necessary to ensure their good performance and service life.
Our factory business: carbide parts, mold parts, medical injection molds, precision injection molds, teflon PFA injection molding, PFA tube fittings. email: [email protected],whatsapp:+8613302615729.