Exploring the Versatile Applications of Precision Tungsten Carbide Bushings
Tungsten Carbide bushings shine brightly in the realms of punching and stretching applications. Widely utilized in the production of cutting tools such as turning tools, milling cutters, planing tools, drills, […]
Tungsten Carbide bushings shine brightly in the realms of punching and stretching applications. Widely utilized in the production of cutting tools such as turning tools, milling cutters, planing tools, drills, and boring tools, they effortlessly tackle the machining of materials ranging from cast iron, non-ferrous metals, plastics, chemical fibers, graphite, glass, stone, and ordinary steel to more challenging materials like heat-resistant steels, stainless steels, high-manganese steels, and tool steels. The cutting speeds of novel Tungsten Carbide cutting tools now rival those of carbon steels by hundreds of times.
The primary role of Tungsten Carbide bushings lies in their protective function for equipment. By employing bushings, wear between punches or bearings and the equipment is effectively minimized, while also serving as a guiding mechanism. In punching molds, Tungsten Carbide bushings, renowned for their durability and high surface finish, require less frequent replacement, thereby enhancing both equipment utilization and personnel efficiency, making them widely adopted.
Our factory business: carbide parts, mold parts, medical injection molds, precision injection molds, teflon PFA injection molding, PFA tube fittings. email: [email protected],whatsapp:+8613302615729.
In stretching applications, particularly for copper and stainless steel components, Tungsten Carbide bushings face challenges such as frequent use-induced heat generation and wear, which can lead to punch misalignment, dimensional inaccuracies, and aesthetic defects in products.
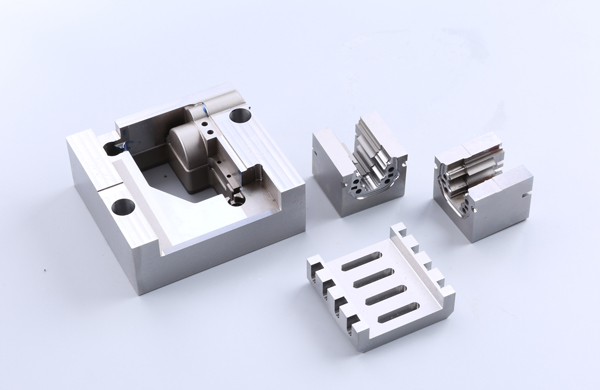
As oil extraction volumes increase and shallow reserves dwindle, the push towards deep wells and highly deviated wells intensifies, necessitating components with superior wear resistance, corrosion resistance, and impact resistance for oil exploration.
Tungsten Carbide bushings, as wear-resistant components in oilfield machinery, boast high hardness, excellent wear resistance, and a superior surface finish, finding increasingly widespread applications in modern society to meet both daily and specialized performance needs. Some enterprises adopt spray welding processes to enhance the durability and service life of Tungsten Carbide bushings.
Post-spray welding, Tungsten Carbide bushings can achieve a hardness of up to HRC60, further improving their wear resistance to meet the demands of the oil machinery industry. However, subsequent turning processes are required to ensure compliance with dimensional and precision requirements specified in drawings.
Currently, common cutting tool materials include Tungsten Carbide, ceramics, and cubic boron nitride (CBN). Given the hardness of Tungsten Carbide bushings, Tungsten Carbide cutting tools are not suitable, while ceramic tools, though ideal for high-hardness workpieces, are limited to small-allowance finishing operations. Consequently, CBN cutting tools stand out as the most suitable choice for processing Tungsten Carbide bushings.