Exploring the Deformation of Tungsten Carbide Products
I. Introduction Tungsten carbide, with its high hardness, excellent wear resistance, and outstanding thermal stability, plays a pivotal role in industrial production. However, Tungsten carbide products occasionally experience deformation in […]
I. Introduction
Tungsten carbide, with its high hardness, excellent wear resistance, and outstanding thermal stability, plays a pivotal role in industrial production. However, Tungsten carbide products occasionally experience deformation in practical applications, which not only impairs their appearance and performance but may also adversely affect production efficiency and product quality. This article delves into the causes of deformation in Tungsten carbide products and proposes feasible solutions.
II. Analysis of the Causes of Deformation in Tungsten Carbide Products
(A) Material Factors
Our factory business: carbide parts, mold parts, medical injection molds, precision injection molds, teflon PFA injection molding, PFA tube fittings. email: [email protected],whatsapp:+8613302615729.
- Carbon Gradient Issue: During the dewaxing, presintering, and sintering processes of Tungsten carbide, changes in carbon content lead to the formation of a carbon gradient. If the concentration of CXHY compounds in the H2 sintering atmosphere is too high, or if the carbon content in the filler is excessive, especially when producing large or “long, flat” products, uneven “decarburization” or “carburization” across different parts results in differential shrinkage, leading to product deformation and bending.
- Cobalt Gradient Influence: During vacuum sintering, the wettability of cobalt on the surface of the graphite boat has a significant impact on the product’s shape. Poor wettability causes the cobalt liquid to move upwards, increasing the surface tension on the top of the product and decreasing it on the bottom, resulting in an upward convex shape. Conversely, good wettability leads to the cobalt liquid moving downwards, increasing the surface tension on the bottom of the alloy and causing the product to concave downwards.
(B) Process Factors
- Temperature Gradient: Uneven temperature distribution during the production process leads to uneven stress distribution within the product, causing deformation. Rapid cooling also exacerbates material inhomogeneity, leading to deformation.
- Density Gradient in Pressed Products: Uneven density distribution during the pressing process results in uneven shrinkage during sintering, causing deformation. Therefore, process parameters such as pressure and holding time need to be strictly controlled.
- Improper Loading into the Boat: Issues such as incorrect boat size or poor contact between the boat and the product during loading can lead to product deformation. Careful inspection of boat size and contact is necessary.
- Differences in Shrinkage Coefficients: When multiple materials with significantly different shrinkage coefficients are used in the production of Tungsten carbide products, deformation is likely to occur. Materials with similar shrinkage coefficients should be selected.
(C) Usage Factors
Prolonged use at high temperatures or exposure to excessive impact forces can lead to deformation of Tungsten carbide products. Therefore, attention should be paid to the usage environment and stress conditions.
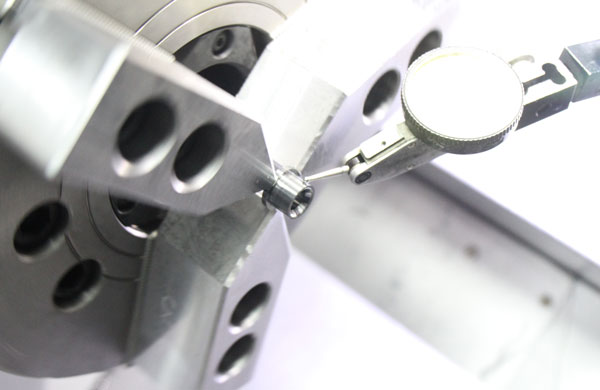
III. Solutions
To address the aforementioned causes of deformation, the following solutions are proposed:
- Optimize Material Formulas and Process Parameters: Adjust formulas and process parameters to reduce the impact of carbon and cobalt gradients on product shape and ensure even stress distribution within the product.
- Strengthen Boat Loading Management: Strictly manage and inspect the boat loading process to ensure accuracy and avoid deformation issues caused by improper loading.
- Strictly Control Usage Conditions: Avoid prolonged use at high temperatures or exposure to excessive impact forces.
- Adopt Advanced Inspection Methods: Use advanced inspection methods such as X-ray inspection and ultrasonic testing to promptly identify and address internal defects and uneven stress distribution issues.
IV. Conclusion
The deformation of Tungsten carbide products is a complex issue influenced by materials, processes, and usage. By thoroughly analyzing the causes and implementing corresponding solutions, the occurrence of deformation can be effectively reduced, improving product quality and performance. Simultaneously, continuous exploration and innovation are needed to drive the continuous progress and development of Tungsten carbide material technology.