Exploring the Categories of Tungsten Carbide Materials: A Comprehensive Analysis of Characteristics
Introduction In the vast realm of materials science, tungsten carbide shines like a brilliant star. As a typical representative of hard alloys, it boasts outstanding characteristics such as high hardness, […]
Introduction
In the vast realm of materials science, tungsten carbide shines like a brilliant star. As a typical representative of hard alloys, it boasts outstanding characteristics such as high hardness, excellent wear resistance, and remarkable thermal stability. These properties make it play a crucial role in numerous fields, including metal processing, mining, and aerospace. Tungsten carbide comes in a wide variety of types, and its classification methods are also diverse. This article will delve deeply and systematically into the categories of tungsten carbide materials, combined with specific figures and information, to provide readers with a clear understanding.
Basic Characteristics of Tungsten Carbide
Tungsten carbide, also known as hard alloy, is mainly composed of tungsten carbide (WC) and a metal binder (such as cobalt, Co). Among them, tungsten carbide constitutes the majority of the tungsten carbide composition, endowing it with high hardness and excellent wear resistance. The metal binder, on the other hand, plays a vital role in bonding the tungsten carbide particles together while imparting a certain degree of toughness and impact resistance to the tungsten carbide. In terms of hardness, tungsten carbide performs exceptionally well, with a hardness range of 89 – 95HRA. Regarding its melting point, tungsten carbide generally has a melting point between 1700℃ and 1900℃, and some special materials can even have a melting point as high as around 3600℃. These outstanding characteristics make tungsten carbide an indispensable key material in many industrial fields.
Our factory business: carbide parts, mold parts, medical injection molds, precision injection molds, teflon PFA injection molding, PFA tube fittings. email: [email protected],whatsapp:+8613302615729.
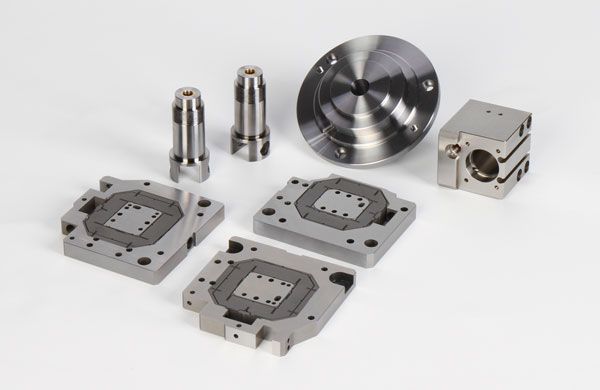
Categories of Tungsten Carbide Materials
Classification by Composition
- Tungsten Carbide – Cobalt (WC – Co): This is the most common type of tungsten carbide. Here, WC represents tungsten carbide, and Co represents cobalt. Cobalt, as a binder, plays a key role in enhancing the plasticity and toughness of tungsten carbide. Tungsten carbide – cobalt exhibits excellent hardness, wear resistance, and impact resistance, making it widely used in cutting tools, molds, and other fields. For example, in the machining industry, cutting tools made of tungsten carbide – cobalt can efficiently cut various metal materials, greatly improving processing efficiency and quality.
- Tungsten Nitride Carbide – Cobalt (WN – Co): Based on tungsten carbide – cobalt, nitrogen is added to further improve the material’s hardness and wear resistance. Tungsten nitride carbide – cobalt is suitable for applications requiring higher hardness and wear resistance, such as high – speed cutting tools. In the aerospace field, some high – speed rotating cutting components made of tungsten nitride carbide – cobalt can maintain stable performance under extreme conditions, ensuring processing accuracy and efficiency.
- Tungsten Carbonitride Carbide – Cobalt (WC – Co – N): This type of tungsten carbide combines the advantages of tungsten carbide – cobalt and tungsten nitride carbide – cobalt, possessing higher hardness, strength, and wear resistance. In fields requiring higher performance, such as precision mold manufacturing and high – end cutting processing, tungsten carbonitride carbide – cobalt demonstrates excellent performance and can meet the usage requirements under complex working conditions.
Classification by Application
- Tool – Grade Tungsten Carbide: Mainly used for manufacturing cutting tools, molds, etc., it has high hardness, high wear resistance, and high thermal stability. Common tool – grade tungsten carbide products include round bars, tungsten carbide plates, and tungsten carbide strips. In the mold manufacturing industry, molds made of tool – grade tungsten carbide can withstand long – term tests of processes such as stamping and injection molding, ensuring product quality and production efficiency.
- Structural – Grade Tungsten Carbide: Used in the manufacture of structural components in the aerospace, automotive, energy, and other fields, it has properties such as high strength, high toughness, and thermal fatigue resistance. This type of tungsten carbide is usually used to manufacture structural components and parts working in high – temperature environments, such as aircraft engine blades and automotive turbochargers, ensuring the stable operation of equipment under harsh conditions such as high temperature and high pressure.
- Functional – Material – Grade Tungsten Carbide: Used for manufacturing various functional devices, such as electromagnetic windows and heating elements, it has specific functional properties. In the electronics and energy fields, functional – material – grade tungsten carbide plays an important role. For example, it is used to manufacture high – efficiency heating elements, which can improve energy utilization efficiency.
Classification by Production Process
- Fusion – Method Tungsten Carbide: Prepared by melting WC and Co (or Fe, Ni, etc.), it has good plasticity and toughness. The fusion – method tungsten carbide has a relatively simple preparation process and low cost, but its performance is slightly inferior to that of powder – metallurgy – method tungsten carbide. In some applications where the performance requirements are not particularly high, fusion – method tungsten carbide has certain application advantages.
- Powder – Metallurgy – Method Tungsten Carbide: Prepared using powder metallurgy technology, it has high density, strength, and wear resistance. Powder – metallurgy – method tungsten carbide has excellent performance, but its preparation process is complex and the cost is high. In high – end manufacturing industries, such as aerospace and precision instrument manufacturing, powder – metallurgy – method tungsten carbide is widely used due to its outstanding performance.
- High – Speed Steel – Tungsten Carbide: Tungsten is added to high – speed steel to improve hardness and wear resistance. High – speed steel – tungsten carbide combines the advantages of high – speed steel and tungsten carbide and is suitable for applications requiring high – speed cutting and wear resistance. In the high – speed cutting field of machining, high – speed steel – tungsten carbide cutting tools can significantly improve cutting speed and processing quality.
Classification by Performance
- High – Strength Tungsten Carbide: With high strength and high toughness, it is suitable for applications subject to high pressure and high loads. In the aerospace and automotive fields, high – strength tungsten carbide is used to manufacture key components, such as aircraft landing gear and automotive drive shafts, ensuring the safety and reliability of equipment under harsh working conditions.
- High – Hardness Tungsten Carbide: With high hardness and high wear resistance, it is suitable for applications with severe wear. For example, tungsten carbide digging teeth and tungsten carbide gun drills used in mining products belong to high – hardness tungsten carbide. In the mining and geological exploration fields, high – hardness tungsten carbide tools can greatly improve work efficiency and service life.
- Thermal – Fatigue – Resistant Tungsten Carbide: With excellent thermal fatigue properties, it is suitable for applications in high – temperature environments. In the energy and aerospace fields, thermal – fatigue – resistant tungsten carbide is used to manufacture high – temperature components, such as gas turbine blades and rocket engine nozzles, which can withstand the action of high – temperature cyclic thermal stress and ensure the long – term stable operation of equipment.
Conclusion
Tungsten carbide, as a crucial hard alloy material, comes in a wide variety of types and has diverse classification methods. By classifying it according to composition, application, production process, and performance, we can gain a clearer and more in – depth understanding of the types and characteristics of tungsten carbide. Different types of tungsten carbide have unique performance and application scenarios. In practical applications, we can choose the appropriate tungsten carbide material according to specific needs to fully utilize its advantages and meet the industrial requirements of different fields.