Exploration of the Main Characteristics of Tungsten Carbide Molds
Tungsten carbide molds, as a shining star in the modern mold manufacturing industry, play a core role in the field of high-precision and high-quality mold manufacturing due to their unique […]
Tungsten carbide molds, as a shining star in the modern mold manufacturing industry, play a core role in the field of high-precision and high-quality mold manufacturing due to their unique physical and chemical properties. This article will comprehensively analyze the main characteristics of tungsten carbide molds, providing readers with an in-depth and comprehensive understanding.
I. Introduction
Our factory business: carbide parts, mold parts, medical injection molds, precision injection molds, teflon PFA injection molding, PFA tube fittings. email: [email protected],whatsapp:+8613302615729.
Tungsten carbide molds are meticulously crafted from tungsten carbide material. Tungsten carbide, also known as cemented carbide, is a high-performance composite material with tungsten carbide (WC) as the main component, incorporated with an appropriate amount of cobalt (Co) or other metallic elements. Its high hardness, high wear resistance, and high corrosion resistance make it shine in the mold manufacturing field.
II. The Four Major Characteristics of Tungsten Carbide Molds
- High Hardness and Wear Resistance
- The hardness of tungsten carbide molds is excellent, with a common hardness range of HRC60~67, and some even exceeding HRC70. This high hardness enables the molds to withstand high-pressure and high-temperature environments, maintaining precision and dimensional stability. The high wear resistance extends the service life of the molds.
- Excellent Heat Resistance
- Tungsten carbide molds can maintain their hardness and rigidity at high temperatures, without easily softening or deforming. In applications such as injection molds that need to withstand high-temperature plastic melts, their heat resistance is particularly important.
- Good Corrosion Resistance
- The tungsten and cobalt components endow tungsten carbide molds with excellent corrosion resistance. When exposed to corrosive media such as acids and alkalis, the mold surface can maintain its smoothness and precision, ensuring performance.
- Excellent Machinability
- Although tungsten carbide has low toughness and is difficult to machine, advanced machining technologies enable precise machining, meeting the manufacturing needs of high-precision and high-quality molds.
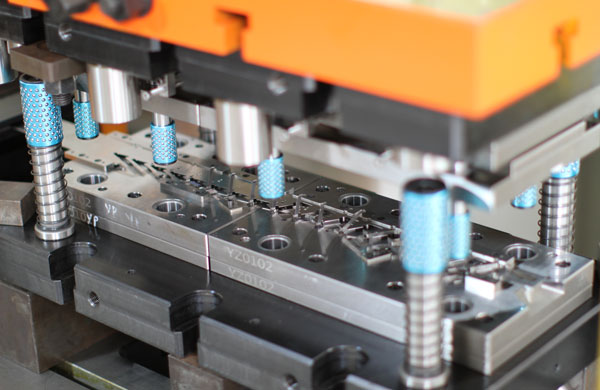
III. Wide Range of Applications and Manufacturing Processes
Tungsten carbide molds are widely used in plastic molds, die-casting molds, injection molds, as well as cemented carbide molds, cold heading dies, cold punching dies, wire drawing dies, and other fields due to their outstanding characteristics. Their manufacturing processes include powder metallurgy molding, hot extrusion molding, isostatic pressing, etc., among which powder metallurgy molding is the most commonly used, capable of producing tungsten carbide molds with complex shapes and high dimensional accuracy.
IV. Application Case Showcase
- Plastic Molds: Tungsten carbide molds excel in the manufacturing of plastic molds, capable of producing high-precision and high-quality plastic molds, ensuring the quality of plastic products.
- Die-Casting Molds: In the manufacturing of die-casting molds, tungsten carbide molds, with their high hardness and excellent heat resistance, are ideal materials.
V. Conclusion and Outlook
In summary, tungsten carbide molds, with their unique high hardness, high wear resistance, high corrosion resistance, excellent machinability, and wide range of applications, occupy an important position in the mold manufacturing field. With technological advancements and industrial development, the performance of tungsten carbide molds will be further enhanced, and their application fields will become even broader.
Related Posts
- Tungsten Carbide: A Shining Star in Multiple Fields
- Which Tungsten Carbide Plate is Good? A Comprehensive Guide and Selection Tips
- Tungsten Carbide with Non-Magnetic Properties: Characteristics, Processing, Applications, and Future Development
- Tungsten Carbide Procurement: Ensuring Authenticity is Crucial