Exploration of Fixation Methods for Tungsten Carbide Punches
Tungsten Carbide punches play a crucial role in blanking products, with their shape directly determining the final form of the blanked product. When designing Tungsten Carbide punches, two major standards […]
Tungsten Carbide punches play a crucial role in blanking products, with their shape directly determining the final form of the blanked product. When designing Tungsten Carbide punches, two major standards must be followed: one is to design according to the product shape, and the other is to fully consider the clearance between the upper and lower molds. The determination of this clearance is primarily based on characteristics such as the thickness and material of the blanked product.
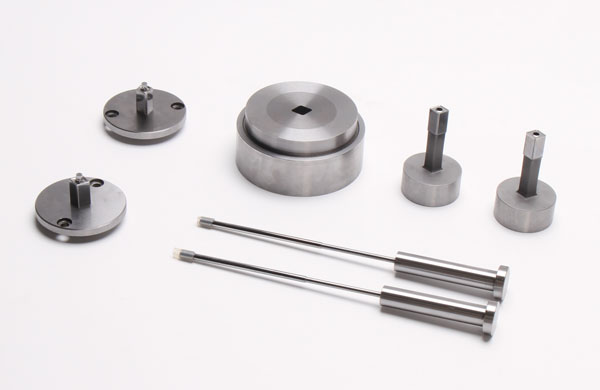
Below are several common fixation methods for Tungsten Carbide punches:
Our factory business: carbide parts, mold parts, medical injection molds, precision injection molds, teflon PFA injection molding, PFA tube fittings. email: [email protected],whatsapp:+8613302615729.
- Fixation with Standard Fixing Plates: Standard fixing plates from brands such as Japan’s MISIMI, Beijing Shimao, and Dalian Panqi can be selected for fixation, which perfectly match the standard Tungsten Carbide punches.
- Fixation with Custom-Made Fixing Plates (Suitable for Space-Constrained Situations): When standard fixing plates cannot be used due to space limitations, custom-made fixing plates can be employed, secured with screws and pins to ensure the stability of the Tungsten Carbide punch.
- Dual Fixation for Large Tungsten Carbide Punches: For larger Tungsten Carbide punches, custom-made fixing plates should be used, secured with screws and pins. Additionally, screws should be used to suspend the punch from the bottom to provide extra support and stability.
- Comprehensive Fixation for Large Tungsten Carbide Punches: For larger Tungsten Carbide punches, apart from using custom-made fixing plates for tightening, set screws should also be applied to the sides of the punch for additional securing, ensuring that the punch remains stationary and does not wobble during the blanking process.