Does Carbide with Cobalt Added Have Better Wear Resistance?
In the grand stage of industrial production, carbide shines like a brilliant star, playing a pivotal role. As a high – performance composite material, it is born from the magical […]
In the grand stage of industrial production, carbide shines like a brilliant star, playing a pivotal role. As a high – performance composite material, it is born from the magical sintering process at high temperatures of metal powders such as tungsten and cobalt. With its outstanding characteristics of high hardness, high strength, and high wear resistance, carbide is widely used in various fields including mechanical processing, mining engineering, and oil drilling. Cobalt, as a key element in carbide, has a significant impact on the alloy’s performance, much like a mysterious magic formula. So, does carbide with cobalt added have better wear resistance? This article will delve into this question.
Basic Characteristics of Carbide and Cobalt
The excellent performance of carbide stems from its unique composition and structure. It is like a highly skilled martial artist, combining a high – hardness carbide phase and a high – toughness metal phase. The carbide phase mainly consists of metal carbides such as tungsten and tantalum. These carbides are like hard armor, with high hardness, high melting points, and good chemical stability. The metal phase is mainly composed of metals such as cobalt and nickel. They are like flexible ribbons, with good toughness and ductility, which can effectively enhance the impact resistance and fracture resistance of carbide.
Our factory business: carbide parts, mold parts, medical injection molds, precision injection molds, teflon PFA injection molding, PFA tube fittings. email: [email protected],whatsapp:+8613302615729.
Cobalt is an indispensable metal – phase component in carbide. It acts like a magical adhesive. Not only does it have excellent toughness and ductility, but it can also form a strong bond with the carbide phase, enhancing the overall performance of carbide. The cobalt content is like a precise seasoning, having a significant impact on the performance of carbide. A reasonable cobalt content can significantly improve the bending strength, toughness, and wear resistance of carbide.
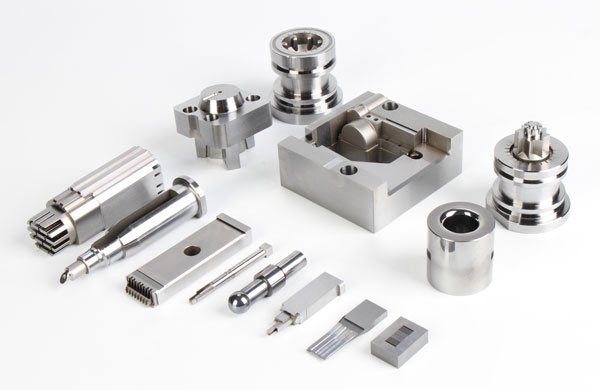
The Influence of Cobalt Content on the Wear Resistance of Carbide
Wear resistance is a key performance indicator of carbide, directly determining its service life and performance stability. The influence of cobalt content on the wear resistance of carbide is mainly reflected in the following aspects:
The Bonding Force between Cobalt and the Carbide Phase
Cobalt plays the role of a binder phase in carbide. It can effectively increase the bonding force between the carbide phases, like strong glue. When the cobalt content is just right, the bonding force between the carbide phases is enhanced, and the wear resistance of carbide also improves. On the contrary, if the cobalt content is too low or too high, it will weaken the bonding force between the carbide phases, thereby affecting the wear resistance of carbide.
The Influence of Cobalt Content on the Toughness of Carbide
Cobalt, as a metal – phase component with excellent toughness, can effectively improve the toughness of carbide, like a solid shield. When carbide is subjected to external impact, the presence of cobalt can disperse the stress, prevent the generation and propagation of cracks, and thus enhance the impact resistance and fracture resistance of carbide. This improvement in toughness helps carbide maintain its integrity during the wear process, thereby improving its wear resistance.
The Influence of Cobalt Content on the Hardness of Carbide
Although the cobalt content has no direct impact on the hardness of carbide, it can indirectly affect the hardness by adjusting the ratio of the carbide phase to the metal phase in carbide. An appropriate cobalt content can balance the ratio of the carbide phase and the metal phase in carbide, allowing it to have both high hardness and good toughness. This balanced state helps improve the wear resistance of carbide.
Experimental Research and Case Studies
To gain a deeper understanding of the influence of cobalt content on the wear resistance of carbide, scholars at home and abroad have conducted a large number of experimental studies and case studies. The results of these studies consistently show that an appropriate cobalt content can significantly improve the wear resistance of carbide.
For example, a research institution conducted wear – resistance tests on carbide with different cobalt contents and found that when the cobalt content is around 8%, the wear resistance of carbide is the best. This is because at this cobalt content, the ratio of the carbide phase to the metal phase in carbide reaches the optimal balance, which not only ensures the hardness of carbide but also improves its toughness. This balanced state allows carbide to maintain a good condition during the wear process, thereby improving its wear resistance.
In addition, some case studies have also shown that in certain specific application scenarios, appropriately increasing the cobalt content can further improve the wear resistance of carbide. For example, carbide drill bits used in the oil – drilling field need to withstand harsh conditions such as high temperature, high pressure, and high – speed wear. Increasing the cobalt content can enhance the impact resistance and fracture resistance of the drill bits, making them more suitable for such harsh environments.
Conclusion and Outlook
In conclusion, carbide with cobalt added does indeed have better wear resistance. An appropriate cobalt content can significantly improve the bonding force between the carbide phases, toughness, and hardness of carbide, thereby enhancing its wear resistance. At the same time, the presence of cobalt can also improve the corrosion resistance and impact resistance of carbide, allowing it to maintain stable performance in various harsh environments.
However, it should be noted that a higher cobalt content is not always better. An excessively high cobalt content can lead to problems such as a decrease in the hardness and density of carbide, thereby affecting its wear resistance. Therefore, in practical applications, an appropriate cobalt content should be selected according to specific operating conditions and requirements.
In the future, with the continuous progress of technology and the development of industrial production, the performance requirements for carbide will become increasingly high. Therefore, how to further optimize the composition and preparation process of carbide to improve its wear resistance and other properties will be one of the important research directions in the future. At the same time, we also need to pay attention to the sustainable utilization of metal resources such as cobalt to provide strong support for the sustainable development of the carbide industry.