Daily Maintenance and Care Guide for Tungsten Carbide Mills
In the manufacturing industry, the efficient maintenance and care of tungsten carbide mills is a crucial aspect that every manufacturer should prioritize. Ultimately, extending the lifespan of mills directly impacts […]
In the manufacturing industry, the efficient maintenance and care of tungsten carbide mills is a crucial aspect that every manufacturer should prioritize. Ultimately, extending the lifespan of mills directly impacts cost control and profit enhancement. Below, we provide a detailed guide on the daily maintenance and care of tungsten carbide mills to help you achieve more efficient production.
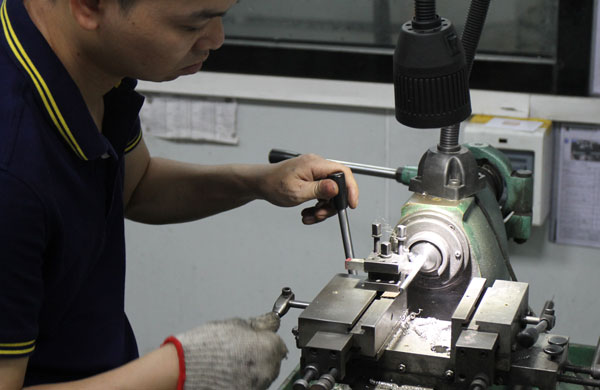
When the axis line of a tungsten carbide mill coincides with or approaches the edge line of a workpiece, operators must pay extra attention to equipment maintenance:
Our factory business: carbide parts, mold parts, medical injection molds, precision injection molds, teflon PFA injection molding, PFA tube fittings. email: [email protected],whatsapp:+8613302615729.
- Inspect Machine Performance: Ensure that the machine’s power and stiffness are sufficient to support the use of the required mill diameter.
- Optimize Tool Overhang: Minimize the overhang of tools on the spindle to reduce the impact of shock loads on the mill axis and workpiece position.
- Select Appropriate Tooth Spacing: Choose the correct tooth spacing for the mill according to process requirements, avoiding excessive blade engagement with the workpiece during cutting to prevent vibration, while ensuring sufficient blade contact during narrow or cavity milling.
- Proper Storage of Mills: When placing mills, avoid contact between the cutting edge and metal objects. In storage, use specialized equipment to maintain spacing between mills, preventing damage to cutting edges. If stacking is necessary, place thick paper between mills. For shank-type mills, insert the shank into a directed, holed plate rack.
- Set Reasonable Feed Rates: Ensure that the feed rate per blade is appropriate, allowing for ideal cutting effects when chips are sufficiently thick and reducing tool wear. Use indexable inserts with positive rake angles for smooth cutting and minimal power consumption.
- Specialized Packaging for Storage: Store mill blades in specialized packaging to prevent damage to cutting edges or model confusion. For sets of gear mills, place them according to specifications, and for those not requiring resharpening after processing, pay attention to cleaning the tooth grooves to prevent dulling and rusting that could affect precision.
- Protect Cutting Edge Precision: The sharpness and integrity of the mill’s cutting edge are crucial for its shape precision. During placement, handling, installation, and disassembly, take special care to protect the precision of the cutting edge.
- Timely Cleanup of Residues: Pay attention to cleaning mills after use, especially those that have used cutting fluids. Promptly remove residual cutting oil and chips to prevent surface oxidation and rusting that could affect precision.
- Apply Rust-Preventive Oil: For long-term unused tools or those in humid working environments, apply rust-preventive oil for protection.
- Protect the Precision of Clamping Areas: The clamping areas of mills have high precision. Any burrs or protrusions on the bottom and clamping surface of sleeve-type mills can directly affect installation precision. Due to the high hardness of mills, repairs are difficult, so special care should be taken during installation, disassembly, placement, and transportation.
- Follow Process Requirements for Storage and Use: Store and use specialized drill-mill machines according to process requirements, and engrave tool numbers on areas that do not affect installation precision.
- Inspect Internal Thread Precision: For cone-shank mills and tool bodies with internal threads at the end, regularly inspect and maintain the precision of the internal threads to prevent accidents during use.
- Follow Maintenance Rules and Monitor Wear: Strictly adhere to tool maintenance and repair rules, and regularly monitor tool wear.
Only by properly maintaining and caring for tungsten carbide mills can their lifespan be effectively extended, and work efficiency improved.