Comprehensive Guide to Tungsten Carbide Machining Considerations
Tungsten carbide, as a high-performance cemented carbide material, is widely used in various fields due to its excellent physical and chemical properties. However, its high hardness and brittleness also pose […]
Tungsten carbide, as a high-performance cemented carbide material, is widely used in various fields due to its excellent physical and chemical properties. However, its high hardness and brittleness also pose challenges for the machining process. This article will comprehensively analyze the key considerations in Tungsten carbide machining.
In the preparation stage before machining, the choice of equipment is crucial. Tungsten carbide machining requires high-rigidity, high-precision, and stable machining equipment, such as high-precision ceramic engraving machines and CNC machining centers. At the same time, the selection of cutting tools is also extremely important. Given the extremely high hardness of Tungsten carbide, cutting tools with high hardness, high wear resistance, and high thermal stability, such as cemented carbide or ceramic cutting tools, must be used. In addition, a detailed machining plan needs to be developed based on the material properties and machining requirements of Tungsten carbide to provide comprehensive guidance for the machining process.
Our factory business: carbide parts, mold parts, medical injection molds, precision injection molds, teflon PFA injection molding, PFA tube fittings. email: [email protected],whatsapp:+8613302615729.
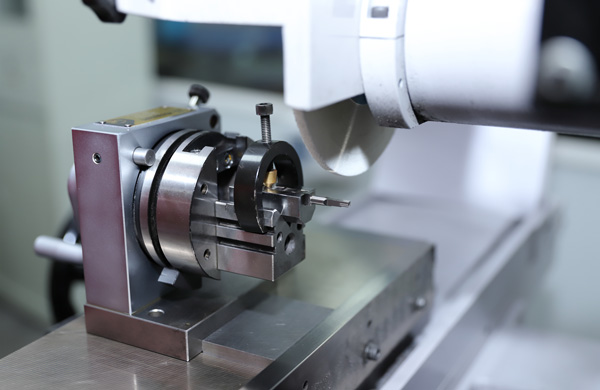
During the machining process, the control of cutting parameters is particularly important. Cutting speed, depth, and feed rate need to be set reasonably according to the characteristics of the equipment, tools, and materials. Too high or too low parameters may affect machining quality and efficiency. At the same time, it is necessary to keep the cutting tools sharp and regularly inspect and replace worn tools. The selection and use of coolant cannot be ignored, as it can effectively reduce cutting temperatures and extend tool life. In addition, measures need to be taken to reduce vibration and deformation during the machining process and avoid excessive impact and overload on the Tungsten carbide.
After machining, a comprehensive inspection of the machined parts is required to ensure they meet the requirements. Waste materials also need to be cleaned up promptly and disposed of in an environmentally friendly manner. The machining equipment needs to be regularly maintained to ensure long-term stable operation.
In summary, Tungsten carbide machining is a task with a high technical threshold. To improve machining quality and efficiency, it is necessary to strengthen technical training and exchanges and introduce advanced technologies and equipment. Only by making adequate preparations, mastering the correct techniques, strengthening equipment maintenance, and improving the skills of personnel can the quality and safety of Tungsten carbide machining be ensured.