Comprehensive Guide to Tungsten Carbide Die Installation
I. Introduction of Tungsten Carbide Die Tungsten carbide dies are indispensable tools in modern industrial production, and their installation process is directly related to the mold’s performance, production efficiency, and […]
I. Introduction of Tungsten Carbide Die
Tungsten carbide dies are indispensable tools in modern industrial production, and their installation process is directly related to the mold’s performance, production efficiency, and safety. To ensure the mold’s normal operation and extend its service life, installation must strictly adhere to operating procedures, paying attention to the details of each step. This article will provide a detailed introduction to the installation process of a tungsten carbide die, focusing on the key points that need attention.
II. Preparation Before Installation: Meticulousness Lays the Foundation
- Inspect the Die: Verify that the die’s model, specifications, and quantity match the production plan, and check for any damage or wear. For new carbide dies, also verify the processing accuracy and surface quality.
- Cleaning Work: Thoroughly clean the mold to remove oil, dust, and rust, thereby improving the mold’s accuracy and stability and reducing wear and failures.
- Prepare Tools: According to the installation requirements, prepare tools such as wrenches, screwdrivers, micrometers, etc., and ensure their accuracy and good condition to facilitate the smooth progress of the installation.
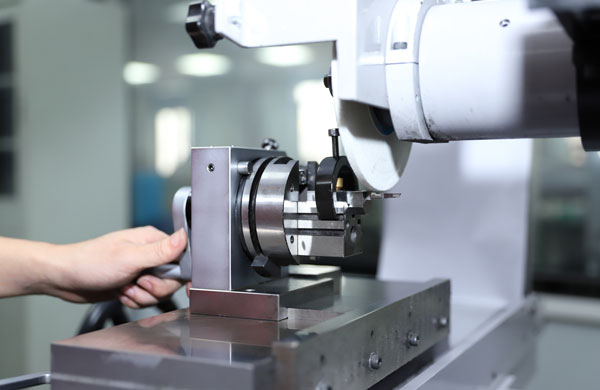
III. Installation Process: Proceed Step by Step to Ensure Precision
- Determine the Installation Position: Based on the production plan and equipment layout, select the mold installation position, ensuring the stability and safety of the equipment to avoid mold damage or personal injury.
- Fix the Die: Place the tungsten carbide die on the equipment workbench and secure it with special fixtures or bolts, paying attention to the tightening force to prevent mold deformation or looseness.
- Adjust the Die Position: According to the equipment’s accuracy requirements and production plan, precisely adjust the mold’s position and angle using appropriate tools and measuring instruments for accurate measurement and positioning.
- Install Guide Devices: For molds that require guiding, install guide devices to ensure the accuracy of mold closing and opening. The installation position and accuracy should meet the design requirements.
- Install Accessories: According to the die’s usage requirements, install accessories such as cooling water pipes, ejector pins, etc., ensuring the accuracy and good condition of the accessories to avoid mold failures or production accidents.
IV. Post-Installation Inspection and Debugging of Tungsten Carbide Die
- Check Die Accuracy: Use measuring tools such as micrometers to check the mold’s parallelism, perpendicularity, coaxiality, etc. Adjust or replace dies that do not meet the requirements.
- Check the Die Fit: Inspect the fit between the die and the equipment, including aspects such as fixation, guiding, and cooling. Adjust or replace relevant parts for poorly fitting areas.
- Debug the Die: Conduct mold debugging on the equipment, including actions such as mold closing, opening, and ejection. Observe whether the mold operates smoothly and check for any abnormal sounds or vibrations.
- Trial Production: After debugging, conduct trial production to verify the mold’s performance and stability. Observe whether the product quality and production efficiency meet the requirements, and make further adjustments and optimizations to the mold based on the actual situation.
V. Notes: Safety First, Accuracy Paramount
- Safe Operation: Strictly adhere to safety operating procedures to ensure the safety of personnel and equipment, avoiding personal injury or equipment damage due to improper operation.
- Accuracy Requirements: The accuracy of tungsten carbide molds is crucial for product quality and production efficiency. Pay special attention to the mold’s accuracy and stability during installation.
- Fit Relationship: The fit relationship between the mold and the equipment affects the mold’s normal operation and stability. Ensure a good and stable fit during installation.
- Cleaning and Maintenance: After installation, clean and maintain the mold to extend its service life and improve production efficiency. Regularly inspect and repair the mold to ensure its normal operation.
VI. Summary: Precise Installation Boosts Production
The installation process of tungsten carbide molds is complex and precise, requiring strict adherence to operating procedures and attention to the details of each step. Through thorough preparation, correct installation steps, comprehensive inspection and debugging, and compliance with notes, the normal operation of tungsten carbide dies can be ensured, their service life can be extended, product quality and production efficiency can be improved, and production costs and failure rates can be reduced.
Our factory business: carbide parts, mold parts, medical injection molds, precision injection molds, teflon PFA injection molding, PFA tube fittings. email: [email protected],whatsapp:+8613302615729.