Comprehensive Analysis of Non-Magnetic Tungsten Carbide
I. Introduction In the ever-evolving field of modern industry, non-magnetic tungsten carbide, as an outstanding hard alloy material, has shone brightly in numerous industries with its unique non-magnetic properties, extremely […]
I. Introduction
In the ever-evolving field of modern industry, non-magnetic tungsten carbide, as an outstanding hard alloy material, has shone brightly in numerous industries with its unique non-magnetic properties, extremely high hardness, and excellent wear resistance, demonstrating wide application potential. This article will provide a comprehensive and in-depth exploration of the definition, production process, characteristics, application fields, and processing technologies of non-magnetic tungsten carbide, aiming to present readers with a thorough understanding.
II. Definition Overview of Non-Magnetic Tungsten Carbide
Non-magnetic tungsten carbide, abbreviated as non-magnetic carbide, is a tungsten carbide material that remains non-magnetized in magnetic field environments. Its magnetic permeability is significantly lower than that of air, thus possessing excellent non-magnetic properties. This material is mainly composed of alloy elements such as WC-Ni-Cr-Ta-Ti-VC, and is sintered in a high-temperature vacuum environment at 1300~1450℃ through advanced powder metallurgy techniques. It is worth noting that its alloy composition is completely free of magnetic substances such as iron, cobalt, and nickel, thereby ensuring stable non-magnetic performance.
Our factory business: carbide parts, mold parts, medical injection molds, precision injection molds, teflon PFA injection molding, PFA tube fittings. email: [email protected],whatsapp:+8613302615729.
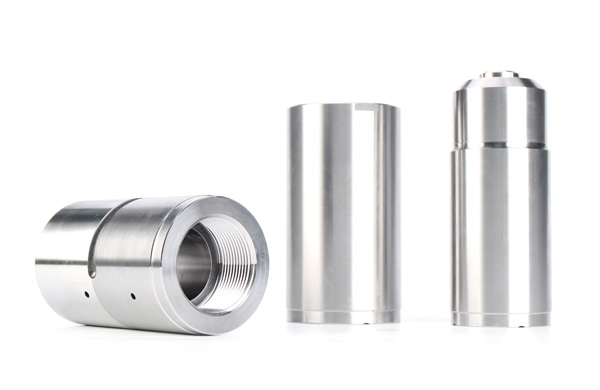
III. Production Process Flow of Non-Magnetic Tungsten Carbide
The production process of non-magnetic tungsten carbide is rigorous and precise, mainly including the following key steps:
- Ingredient Preparation: Accurately weigh and mix raw materials such as WC, TiC, TaC, Co, and VC in proportion to ensure uniform composition.
- Crushing and Drying: Finely crush the mixed raw materials and thoroughly remove moisture through a drying process.
- Sieving and Shaping: Sieve the dried powder, add a shaping agent, dry again, and then press into shape to form preliminary blanks.
- High-Temperature Sintering: Place the blanks in a high-temperature vacuum sintering furnace, and after high-temperature and high-pressure sintering, obtain dense non-magnetic tungsten carbide products.
- Quality Inspection: Adopt advanced techniques such as non-destructive ultrasonic testing to strictly inspect the sintered products and ensure excellent quality.
IV. Unique Characteristics of Non-Magnetic Tungsten Carbide
Non-magnetic tungsten carbide stands out with its unique properties, mainly manifested in the following aspects:
- Non-Magnetic: Remains non-magnetized in magnetic fields, with extremely low magnetic permeability and excellent non-magnetic properties.
- High Hardness: The hardness range is typically between 88.0~92.5 HRA, adjustable according to application requirements.
- High Bending Strength: After high-temperature and high-pressure vacuum sintering, it possesses outstanding bending strength.
- Long Service Life: Thanks to its high hardness and bending strength, tools made from it have a long service life.
- Excellent Processing Performance: During processing, it is not prone to issues such as mold wall galling, mold cavity deformation, and powder adhesion, ensuring product dimensional accuracy and surface quality.
V. Wide Application Fields of Non-Magnetic Tungsten Carbide
Non-magnetic tungsten carbide, with its unique properties, is widely used in multiple industries:
- Precision Manufacturing: It has become the preferred material for manufacturing high-precision products, such as battery mold burner nozzles, tungsten and molybdenum clamps, and glass cutting tools.
- Electronic Products: Suitable for the manufacture of electronic products in non-magnetic or low-magnetic environments, such as inductor coils, transformers, and relay cores.
- Medical Devices: Plays an important role in medical equipment such as Magnetic Resonance Imaging (MRI), avoiding interference with diagnostic results.
- Military and Aerospace: Has important applications in the defense industry, such as making special protective layers with strong magnetic permeability and no obstruction to magnetic force.
- Other Fields: Also widely used in watch manufacturing, construction, power, electronics, chemical industry, rail transit, and metal processing, among others.
VI. Processing Technologies of Non-Magnetic Tungsten Carbide
As a high-hardness material, non-magnetic tungsten carbide requires professional methods for processing:
- Mechanical Processing: Use diamond and other superhard material tools for milling, turning, and drilling, with processing speeds controlled to protect the tools and ensure surface quality.
- Electrical Discharge Machining (EDM): Suitable for creating tiny holes or contours, with precise control of processing speed and energy to prevent steel deformation or surface degradation.
- Laser Processing: Can be used for cutting, drilling, and surface treatment processes, with strict control of heating time and speed to maintain hardness and prevent deformation.
- Other Processing Methods: Such as chemical etching, plasma cutting, and ultrasonic processing, can be flexibly chosen according to specific needs.
VII. Conclusion
Non-magnetic tungsten carbide, as a representative of high-performance hard alloy materials, demonstrates its irreplaceable application value in multiple fields. Its unique non-magnetic properties, high hardness, and wear resistance make it an ideal choice for manufacturing high-precision, high-quality products. With the continuous advancement of technology and the thriving development of the manufacturing industry, the application prospects of non-magnetic tungsten carbide will become even broader, bringing more innovation and breakthroughs to various industries.