Comprehensive Analysis of Causes and Solutions for Internal Leakage in Tungsten Carbide Valves
Introduction In the grand stage of industrial production, the tungsten carbide valve is like a crucial “gatekeeper”, playing an indispensable role in the field of fluid control with its high […]
Introduction
In the grand stage of industrial production, the tungsten carbide valve is like a crucial “gatekeeper”, playing an indispensable role in the field of fluid control with its high performance. From the precise regulation of chemical processes to the safe transportation of energy, tungsten carbide valves are essential. However, as time goes by, the problem of internal leakage in tungsten carbide valves, like a hidden “reef”, not only disrupts the normal operation of the valve but also poses a serious threat to production safety and product quality. In – depth analysis of the causes of internal leakage in tungsten carbide valves and the exploration of effective solutions have become an important task that technicians in related fields urgently need to tackle. This article will comprehensively analyze the common causes of internal leakage in tungsten carbide valves and propose targeted solutions, aiming to provide valuable references for technicians in the industry.
Causes of Internal Leakage in Tungsten Carbide Valves
Damage to the Sealing Surface
The sealing surface can be regarded as the “heart” of the tungsten carbide valve and the core part for achieving the sealing function. During actual operation, factors such as continuous erosion by the medium, chemical corrosion, and improper operation act like ruthless “killers”, causing wear, scratches, and even deformation on the sealing surface. These damages significantly reduce the flatness and smoothness of the sealing surface, thereby destroying the valve’s sealing performance and leading to internal leakage.
Our factory business: carbide parts, mold parts, medical injection molds, precision injection molds, teflon PFA injection molding, PFA tube fittings. email: [email protected],whatsapp:+8613302615729.
Aging of Sealing Materials
Tungsten carbide valves usually use rubber, plastic, and other polymer materials as sealing materials. However, during long – term service, these materials are comprehensively affected by factors such as temperature, pressure, and the medium, gradually showing phenomena like aging, hardening, and cracking. The degradation of the sealing material’s performance prevents it from closely fitting the sealing surface, resulting in a decrease in sealing performance and the occurrence of internal leakage.
Improper Valve Installation
The installation process of a valve is like a precise “surgery”, and any negligence in any step can lead to serious consequences. If the flange connection is not tight, it is like leaving the city gate unclosed, allowing the medium to easily leak; uneven tightening of the bolts will cause uneven stress on different parts of the valve, affecting the sealing effect; incorrect placement or damage to the sealing gasket will also directly destroy the valve’s sealing performance and cause internal leakage.
Improper Operation and Maintenance
During the use of the valve, the behavior of the operators has a crucial impact on the valve’s performance. Frequent opening and closing of the valve, excessive force, and other operations will subject the valve components to excessive stress, accelerating the wear and damage of the sealing surface; and untimely maintenance, such as not replacing the sealing material on time and not cleaning up impurities, will cause the accumulation of dirt inside the valve, affecting the sealing performance and eventually leading to internal leakage.
Medium – Related Issues
Impurities and particulate matter in the medium are like “invisible killers”. During the operation of the valve, they may cause wear on the sealing surface, destroying its flatness; or block the valve passage, affecting the normal opening and closing of the valve, and thus affecting the valve’s sealing performance and causing internal leakage.
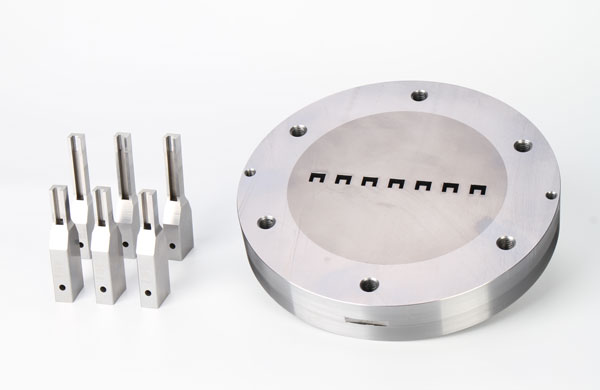
Solutions for Internal Leakage in Tungsten Carbide Valves
Inspect and Repair the Sealing Surface
When internal leakage is found to be caused by damage to the sealing surface, the first task is to carefully inspect the condition of the sealing surface. For minor wear and scratches, fine processes such as grinding and polishing can be used for repair to restore the flatness and smoothness of the sealing surface; for severe deformation and damage, the sealing surface needs to be replaced in a timely manner. During the repair or replacement process, strict quality control must be ensured to make sure the sealing surface meets the design requirements and to guarantee the valve’s sealing performance.
Replace the Sealing Material
If the internal leakage problem is caused by the aging of the sealing material, replacing it with a new one is an effective solution. When selecting a new sealing material, factors such as the nature of the medium, working temperature, and pressure need to be comprehensively considered to choose the most suitable sealing material. At the same time, the replacement process must be carried out strictly according to the operating procedures to ensure that the sealing material is installed correctly and tightly, eliminating potential leakage hazards.
Inspect and Adjust the Valve Installation
For internal leakage caused by improper installation, a comprehensive inspection of the valve’s installation is the key. First, check whether the flange connection is tight and whether the bolts are evenly tightened; then check whether the sealing gasket is placed correctly and whether it is damaged. For the discovered problems, timely adjustments and repairs should be made to ensure that the valve’s installation quality meets the standard requirements.
Standardize Operation and Maintenance
To avoid internal leakage caused by improper operation and maintenance, it is necessary to establish standardized operation and maintenance procedures. Operators must strictly follow the operating procedures and avoid improper operations such as frequent opening and closing and excessive force; maintenance personnel should regularly inspect and replace the sealing material, clean up impurities, etc., to ensure that the valve is always in good operating condition. In addition, strengthening the training and management of operators to improve their professional skills and quality is also an important measure to ensure the normal operation of the valve.
Control the Quality of the Medium
Controlling the quality of the medium is an important link in preventing internal leakage. Before the medium enters the valve, strict filtering and purification treatment should be carried out to remove impurities and particulate matter. At the same time, regular detection and analysis of the medium should be conducted to ensure that it meets the usage requirements. Once the medium is found to have problems, it should be promptly treated and replaced to avoid damage to the valve.
Preventive Measures
In addition to the above solutions, the following preventive measures can be taken to reduce the incidence of internal leakage in tungsten carbide valves:
- Reasonable Selection: Choose the appropriate valve model and specification to ensure that the valve matches the piping system well, avoiding internal leakage caused by excessive pressure or flow on the valve during operation due to improper selection.
- Clean the Piping: Before installing the valve, thoroughly clean and inspect the piping system to remove impurities and particulate matter in the pipe, creating a good environment for the normal operation of the valve.
- Regular Inspection: Regularly inspect and maintain the valve and establish detailed inspection records to promptly discover and deal with potential problems, nipping the hidden dangers of internal leakage in the bud.
- Strengthen Training: Strengthen the training and management of operators to improve their operation skills and safety awareness, so that they can operate the valve correctly and standardly, reducing internal leakage problems caused by human factors.
- Improve the System: Establish a sound valve management system and operating procedures, clarify the responsibilities of each department and personnel, and ensure that there are rules to follow for the correct use and maintenance of the valve.
Conclusion
Internal leakage in tungsten carbide valves is a common problem in industrial production, and its causes are complex and diverse. Through in – depth analysis of the causes of internal leakage and research on solutions, we can effectively reduce the incidence of internal leakage, improve the reliability and service life of the valve. At the same time, strengthening the formulation and implementation of preventive measures is also an important means to ensure the normal operation of the valve and reduce the incidence of internal leakage. As a professional tungsten carbide machining manufacturer, Yize Mould will continue to deeply explore solutions and preventive measures for internal leakage problems in tungsten carbide valves, continuously improve its technical level and service quality, and contribute more to the safety and stability of industrial production.