Complete Guide to Tungsten Carbide Mold Installation
Tungsten carbide molds are highly favored in the mold manufacturing industry for their excellent performance. However, their installation process cannot be overlooked. The following is a brief overview of the […]
Tungsten carbide molds are highly favored in the mold manufacturing industry for their excellent performance. However, their installation process cannot be overlooked. The following is a brief overview of the entire process of installing tungsten carbide molds.
Before installation, thorough preparation is necessary. First, carefully inspect the mold for completeness, ensuring there are no cracks or defects. Next, use a cleaner to thoroughly clean the mold surface, removing oil and dust. Finally, verify the mold’s dimensional accuracy to ensure it meets the requirements.
Our factory business: carbide parts, mold parts, medical injection molds, precision injection molds, teflon PFA injection molding, PFA tube fittings. email: [email protected],whatsapp:+8613302615729.
During installation, selecting the appropriate tools and equipment is crucial. After determining the mold’s installation position and orientation, carefully lift the mold into the predetermined position and securely fasten it using locating pins and pressure plates. Throughout this process, strictly adhere to operating procedures to avoid damaging the mold due to excessive force.
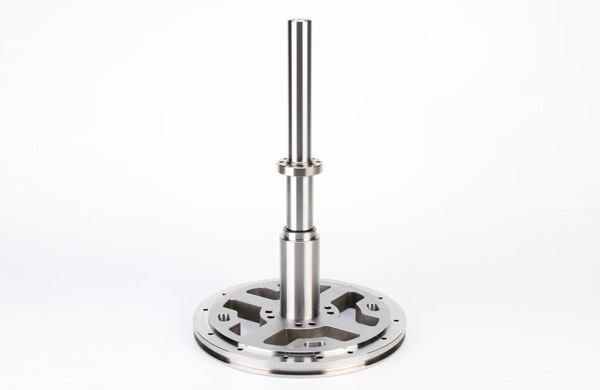
During installation, it is also important to protect the mold from collisions and scratches. Additionally, ensure that the mold is fully compatible with the equipment, and pay attention to the ambient temperature and humidity to avoid affecting the mold’s performance.
After installation, maintenance and care are equally important. Regularly check the mold’s tightness, keep the surface clean, lubricate moving parts to reduce wear, and promptly replace or repair any worn or damaged parts.
In summary, the installation of tungsten carbide molds requires meticulous attention to detail, from preparation to installation, and subsequent maintenance. Only in this way can the mold’s performance be fully utilized, providing strong support for manufacturing processes.