Complete Guide to Tungsten Carbide Die Installation: Details Determine Success
Tungsten carbide dies, with their high hardness and wear resistance, play a vital role in industrial production. However, their installation process requires extreme caution. This article will outline the key […]
Tungsten carbide dies, with their high hardness and wear resistance, play a vital role in industrial production. However, their installation process requires extreme caution. This article will outline the key steps and precautions for installing tungsten carbide dies.
Before installation, thorough preparations are essential. First, the die must be fully inspected to ensure that the surface is free of cracks and burrs, and that the dimensions and specifications match the equipment. Fasteners and connecting parts must also be complete and in good condition. Second, the die and installation area need to be thoroughly cleaned to remove oil, dirt, and other impurities, ensuring good contact. Furthermore, tungsten carbide dies are sensitive to temperature and should be stored in a constant temperature environment of 25-30°C. Finally, preheating treatment is necessary to eliminate internal stress in the die and improve its toughness and wear resistance.
Our factory business: carbide parts, mold parts, medical injection molds, precision injection molds, teflon PFA injection molding, PFA tube fittings. email: [email protected],whatsapp:+8613302615729.
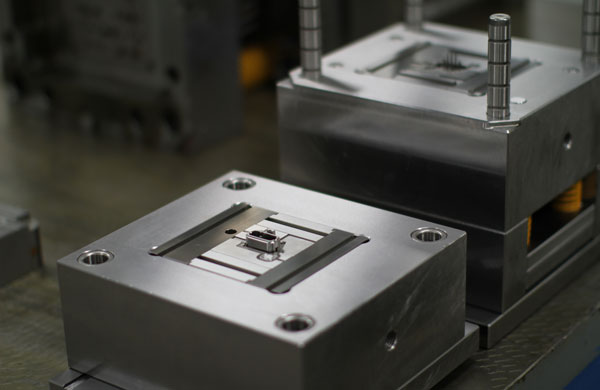
During installation, precise installation is the top priority. Use specialized tools and equipment, and follow the operating procedures to ensure accurate fit between the die and the equipment. The fit clearance should be adjusted appropriately to avoid being too tight or too loose. At the same time, lubricate the contact surface between the die and the equipment to reduce friction and wear. It is strictly prohibited to use a hammer or other hard objects to strike the die, as this can cause cracks or deformation. Operators must strictly follow safety operating procedures and wear personal protective equipment.
After installation, debugging and inspection are equally important. Debug the equipment to observe the fit between the die and the equipment and the operating status of the equipment. Conduct a comprehensive inspection of the die to ensure it is securely fixed, the fasteners are tight, and the connecting parts are intact. Before putting the die into use, it needs to be lubricated to reduce friction and wear. Finally, conduct a trial run to observe the working status of the die and the operation of the equipment, ensuring that the die operates stably and achieves the expected processing results.
In summary, the installation of tungsten carbide dies must strictly follow operating procedures and safety requirements to ensure the safe and stable operation of the die and improve production efficiency.
Related Posts
- Key Considerations for Tungsten Carbide Component Machining and Future Prospects
- Tungsten Carbide Parts: The Shining Pearl of Industrial Manufacturing
- The Widespread Applications of Tungsten Carbide
- Comprehensive Analysis of Tungsten Carbide Parts: Characteristics, Types, Applications, and Future Trends