Common Problems and Solutions in Carbide Compaction
Carbide, as a high-performance engineering material, is widely used in fields such as cutting tools, mold manufacturing, and mining. Its excellent performance mainly stems from its high hardness, high strength, […]
Carbide, as a high-performance engineering material, is widely used in fields such as cutting tools, mold manufacturing, and mining. Its excellent performance mainly stems from its high hardness, high strength, high wear resistance, and high corrosion resistance. However, in the production process of carbide, compaction, as one of the key processes, often encounters some problems. These problems not only affect the performance of carbide but may also reduce production efficiency. This article will analyze the common problems in the carbide compaction process and propose corresponding solutions.
I. Common Problems in the Carbide Compaction Process
1. Poor Powder Flowability
The flowability of carbide powder is an important factor affecting the compaction effect. Powder with poor flowability is prone to uneven distribution during the compaction process, leading to problems such as uneven product density and poor dimensional accuracy. The reasons for poor flowability may include uneven powder particle size distribution, irregular powder shape, and excessive powder moisture content.
Our factory business: carbide parts, mold parts, medical injection molds, precision injection molds, teflon PFA injection molding, PFA tube fittings. email: [email protected],whatsapp:+8613302615729.
2. Uneven Compaction Force
The compaction force is one of the key factors in the carbide compaction process. Uneven compaction force will result in uneven internal stress distribution in the product, causing defects such as cracks and deformation. The reasons for uneven compaction force may include unreasonable mold design, insufficient press accuracy, and too fast or too slow compaction speed.
3. Severe Mold Wear
The mold is a key component in the carbide compaction process, and its quality directly affects the accuracy and surface quality of the product. Severe mold wear will lead to problems such as decreased product dimensional accuracy and increased surface roughness. The reasons for mold wear may include improper material selection, unreasonable mold structure design, and poor lubrication.
4. Difficult Product Demolding
Difficult product demolding is a common problem in the carbide compaction process. Demolding difficulties will not only affect production efficiency but may also cause product damage. The reasons for demolding difficulties may include unreasonable mold design, excessive friction between the product and the mold, and inconsistent product shrinkage rates.
5. Internal Cracks in the Product
Internal cracks in the product are a serious problem in the carbide compaction process. The presence of cracks will greatly reduce the strength and wear resistance of the product. The reasons for crack generation may include uneven compaction force, poor powder quality, and improper mold temperature control.
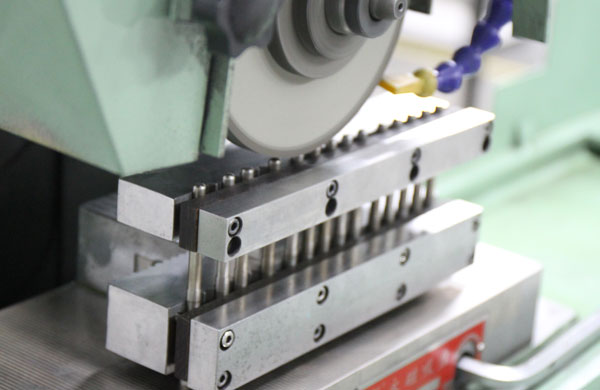
II. Strategies to Solve Common Problems in Carbide Compaction
1. Improve Powder Flowability
To address the problem of poor powder flowability, the flowability of the powder can be improved by optimizing the powder preparation process. For example, controlling the powder particle size distribution, improving the powder shape, and reducing the powder moisture content. In addition, some measures can be taken during the compaction process to improve powder flowability, such as using lubricants and improving the compaction environment.
2. Optimize the Compaction Process
To solve the problem of uneven compaction force, the compaction process can be optimized. First, ensure that the mold design is reasonable and the mold accuracy meets the requirements. Second, select a suitable press and control the compaction speed and pressure. In addition, processes such as pre – compaction and segmented compaction can be used to improve the internal stress distribution of the product.
3. Improve Mold Design
To address the problem of severe mold wear, the mold design can be improved to extend the mold service life. First, choose mold materials with good wear resistance, such as carbide steel and ceramics. Second, reasonably design the mold structure to reduce the friction between the mold and the product. In addition, surface treatment technologies can be used to improve the wear resistance and corrosion resistance of the mold.
4. Improve Lubrication Conditions
To solve the problem of difficult product demolding, the lubrication conditions can be improved. First, ensure that the mold surface finish meets the requirements to reduce the friction between the product and the mold. Second, lubricants can be applied to the mold surface or lubricating films can be used to reduce friction. In addition, the shrinkage rate of the product can be adjusted to improve the demolding performance.
5. Strengthen Quality Control
To address the problem of internal cracks in the product, quality control needs to be strengthened. First, ensure that the powder quality meets the requirements and avoid using powder containing impurities or of poor quality. Second, control parameters such as temperature and pressure during the compaction process to avoid excessive internal stress. In addition, post – treatment processes such as heat treatment can be used to eliminate residual stress inside the product.
III. Future Development of Carbide Compaction Technology
With the progress of science and technology and the development of industry, carbide compaction technology is constantly being innovated and improved. The future development trends of carbide compaction technology will mainly be reflected in the following aspects:
1. Intelligent Compaction Technology
Utilize artificial intelligence and big data technology to achieve intelligent control of the carbide compaction process. Through real – time monitoring and data analysis, optimize compaction parameters and processes to improve the accuracy and performance of the product.
2. Green and Environmentally Friendly Compaction Technology
Develop environmentally friendly compaction processes and materials to reduce energy consumption and emissions during the production process. Use recyclable mold materials and lubricants to achieve green production.
3. Precision Compaction Technology
Improve the accuracy and surface quality of carbide products. Use high – precision molds and advanced compaction equipment to achieve precision production of products.
4. Customized Compaction Technology
Develop customized carbide products according to customer needs. By adjusting parameters such as powder composition and compaction process, produce carbide products with specific performance that meet customer requirements.
In conclusion, there are various common problems in the carbide compaction process, but these problems can be effectively solved through measures such as optimizing the process, improving mold design, and strengthening quality control. In the future, carbide compaction technology will develop in the direction of intelligence, green environmental protection, precision, and customization, providing strong support for the sustainable development of the carbide industry.