Common Problems and Causes in Tungsten Carbide Pressing
Tungsten carbide, also known as cemented carbide, plays a crucial role in many fields such as mechanical processing, mold manufacturing, and mining tools due to its excellent properties like high […]
Tungsten carbide, also known as cemented carbide, plays a crucial role in many fields such as mechanical processing, mold manufacturing, and mining tools due to its excellent properties like high hardness, high wear resistance, and high elastic modulus. However, during the pressing process of tungsten carbide, various problems are often encountered, which not only affect product quality but also reduce production efficiency. Next, this article will comprehensively and deeply explore the common problems and their causes in the tungsten carbide pressing process.
Common Problems in Tungsten Carbide Pressing
Uneven Pressing Density
During the pressing of tungsten carbide, uneven pressing density is a common phenomenon. It is manifested as significant density differences within the product or between different parts, leading to unstable product performance. For example, in some tungsten carbide components that require high density uniformity, uneven density may cause localized excessive wear and inconsistent strength during use.
Our factory business: carbide parts, mold parts, medical injection molds, precision injection molds, teflon PFA injection molding, PFA tube fittings. email: [email protected],whatsapp:+8613302615729.
Pressing Cracking
Cracking sometimes occurs during the tungsten carbide pressing process. Cracking not only damages the product’s appearance, causing obvious cracks on the surface, but also significantly reduces the product’s performance and may even lead to product rejection. For instance, in some high – precision machining tungsten carbide tools, cracking will make them unable to function properly.
Deformation after Pressing
The pressed tungsten carbide products may sometimes deform. Deformation can reduce the dimensional accuracy of the product, making it unable to meet the usage requirements. For example, when manufacturing tungsten carbide molds, deformation may prevent the mold from accurately fitting with the workpiece, affecting the machining accuracy.
Surface Defects during Pressing
Surface defects such as scratches, dents, and bubbles may also appear during the tungsten carbide pressing process. These defects not only affect the product’s appearance but also reduce its performance. For example, tungsten carbide parts with surface defects may accelerate wear when in contact with other components.
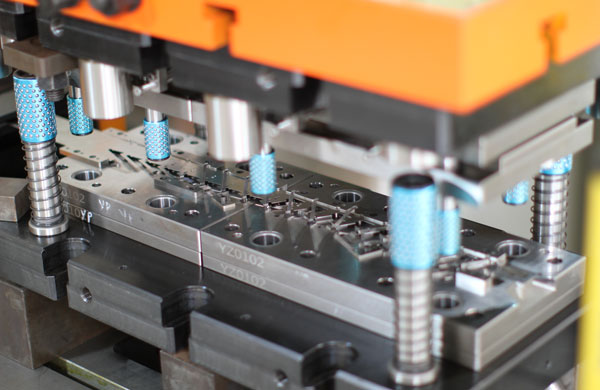
Analysis of the Causes of Tungsten Carbide Pressing Problems
Poor Powder Flowability
The flowability of tungsten carbide powder has a critical impact on the pressing density. When the powder flowability is poor, the distribution of the powder in the mold will be uneven, resulting in uneven pressing density. Poor powder flowability may be caused by factors such as uneven particle size distribution, irregular particle shape, and excessive moisture content. For example, if the particle size difference is too large, it will be difficult for small particles to fill the gaps between large particles, affecting flowability.
Unreasonable Mold Design
Unreasonable mold design is also a common factor that causes tungsten carbide pressing problems. Unreasonable mold design may be reflected in an unreasonable structure, insufficient dimensional accuracy, and improper material selection. These problems can lead to uneven powder distribution in the mold, increased friction between the mold and the powder, and shortened mold life. For example, an unreasonable mold structure design may cause the powder to be subjected to uneven forces during the pressing process, resulting in uneven density.
Improper Setting of Pressing Parameters
Improper setting of pressing parameters can also lead to tungsten carbide pressing problems. Pressing parameters include pressing pressure, speed, and temperature. The setting of these parameters directly affects the compaction effect of the powder and the product quality. For example, if the pressing pressure is too low, the powder cannot be fully compacted, resulting in low product density and poor strength; if the pressing speed is too fast, the powder will be compacted before it can fully deform, easily leading to cracks and deformation; if the pressing temperature is too high, the powder is prone to oxidation and sintering phenomena, affecting product quality.
Unclean Pressing Environment
An unclean pressing environment is also one of the causes of tungsten carbide pressing problems. Impurities such as dust and oil in the environment can adhere to the powder surface or the mold surface, affecting the powder’s flowability and the pressing effect. For example, oil stains can cause the powder particles to adhere to each other, reducing flowability.
Uneven Internal Stress Distribution in the Material
During the pressing process, the material is subjected to external forces, resulting in internal stress. When the stress distribution is uneven, the material is prone to cracking and deformation. For example, when pressing tungsten carbide parts with complex shapes, stress differences in different parts may cause the parts to crack.
Measures to Solve Tungsten Carbide Pressing Problems
Optimizing the Powder Preparation Process
By improving the powder preparation process, the flowability of the powder can be improved, and problems such as uneven particle size distribution and excessive moisture content can be reduced, thereby improving the pressing density and product quality. For example, advanced powder screening technology can be used to ensure uniform powder particle size.
Improving the Mold Design
Optimizing the mold structure and dimensional accuracy, and selecting appropriate mold materials can reduce the friction between the mold and the powder, improve mold life and product quality. For example, a reasonable mold cavity structure can be designed according to the product shape and performance requirements.
Reasonably Setting the Pressing Parameters
Based on the specific requirements of the product and the characteristics of the powder, the pressing parameters such as pressing pressure, speed, and temperature should be set reasonably to obtain the ideal pressing effect. For example, the optimal pressing parameters for different specifications of tungsten carbide powder can be determined through experiments.
Keeping the Pressing Environment Clean
Regularly cleaning the workshop and using clean compressed air and other measures can keep the pressing environment clean and reduce the impact of impurities on the pressing effect. For example, air purification equipment can be installed to filter dust and oil stains in the air.
Adding a Heat Treatment Process
By adding a heat treatment process, the internal stress of the material can be reduced, the occurrence of cracking and deformation can be minimized, and the product performance and service life can be improved. For example, after pressing, the tungsten carbide product can be annealed to eliminate internal stress.
Summary
Common problems in the tungsten carbide pressing process include uneven pressing density, cracking, deformation, and surface defects. These problems are caused by various reasons such as poor powder flowability, unreasonable mold design, improper setting of pressing parameters, unclean pressing environment, and uneven internal stress distribution in the material. To solve these problems, measures such as optimizing the powder preparation process, improving the mold design, reasonably setting the pressing parameters, keeping the pressing environment clean, and adding a heat treatment process need to be taken. Through the implementation of these measures, the pressing effect and product quality of tungsten carbide can be effectively improved to meet the needs of various fields for tungsten carbide products.