Common Issues and Causes in Tungsten Carbide Compaction
I. Introduction Tungsten carbide, a type of alloy material synthesized through powder metallurgy by combining hard compounds of refractory metals with binder metals, boasts high hardness, excellent wear resistance, good […]
I. Introduction
Tungsten carbide, a type of alloy material synthesized through powder metallurgy by combining hard compounds of refractory metals with binder metals, boasts high hardness, excellent wear resistance, good strength and toughness, as well as outstanding heat and corrosion resistance. It finds wide application in mold manufacturing, tool production, wear-resistant parts, and various other fields. However, during the compaction process of tungsten carbide, a series of issues often arise, which not only compromise the quality and performance of the products but may also lead to increased production costs. This article aims to comprehensively review the frequent problems encountered in the tungsten carbide compaction process, delve into their causes, and provide valuable references for the production and quality control of tungsten carbide.
II. Common Issues in Tungsten Carbide Compaction
- Uneven Compaction Density
- In the tungsten carbide compaction process, uneven compaction density is a common occurrence, where significant density variations exist among different parts of the product. This inhomogeneity directly leads to fluctuations in product performance, such as variations in hardness and wear resistance.
- Compaction Cracks
- Compaction cracks are a persistent problem in the tungsten carbide compaction process, manifesting as cracks on the surface or within the product. These cracks not only mar the appearance of the product but may also weaken its strength and toughness.
- Dimensional Deviations in Compaction
- Dimensional deviations refer to significant discrepancies between the dimensions of the tungsten carbide product after compaction and the standard dimensions. Such deviations may render the product unsuitable for its intended use or even result in scrap.
- Difficulties in Ejection from the Mold
- During the tungsten carbide compaction process, there are times when the product is difficult to eject from the mold. This not only affects production efficiency but may also cause damage to the mold.
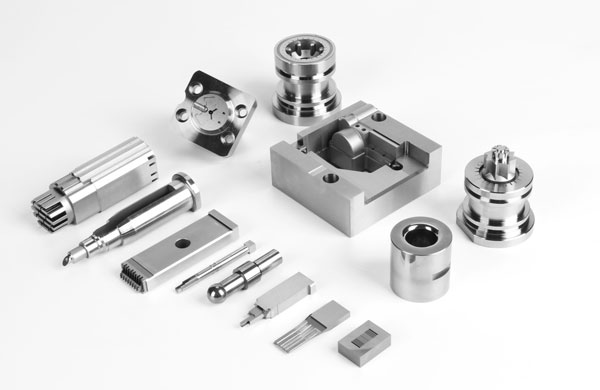
III. Analysis of Causes for Tungsten Carbide Compaction Issues
- Causes of Uneven Compaction Density
- (1) Inhomogeneous Powder Mixing: If the tungsten carbide powder is not mixed uniformly, it will lead to differences in powder composition among different parts, thereby affecting the compaction density.
- (2) Unreasonable Mold Design: The design of the mold cavity, vent holes, and other factors can impact powder filling and compaction. An unreasonable mold design can easily result in uneven compaction density.
- (3) Inappropriate Compaction Process Parameters: Compaction pressure, holding time, compaction speed, and other parameters are crucial for compaction density. Improper parameter settings can lead to uneven compaction density.
- Causes of Compaction Cracks
- (1) Poor Powder Quality: Impurities, pores, and other defects in the powder can weaken the strength and toughness of the material, making it prone to cracking.
- (2) Inadequate Mold Temperature Control: Both excessively high and low mold temperatures can affect the flowability and compaction effect of the powder, leading to the formation of cracks.
- (3) Stress Concentration During Compaction: If the stress distribution is uneven or there is stress concentration during compaction, it can easily lead to the formation of cracks.
- Causes of Dimensional Deviations in Compaction
- (1) Mold Wear: The mold gradually wears during use, leading to changes in the cavity dimensions and resulting in dimensional deviations.
- (2) Mold Assembly Errors: Errors such as inaccurate positioning and loose fastening during mold assembly can all lead to dimensional deviations.
- (3) Fluctuations in Compaction Process Parameters: Fluctuations in parameters such as compaction pressure and holding time can affect the dimensional stability of the product, leading to deviations.
- Causes of Difficulties in Ejection from the Mold
- (1) Unreasonable Mold Design: Inadequate design of the mold’s ejection taper, ejection hole position, and other aspects can easily lead to difficulties in ejection.
- (2) High Surface Roughness of the Mold: A high surface roughness of the mold increases the friction between the product and the mold, causing difficulties in ejection.
- (3) High Compaction Temperature: A high compaction temperature can create a strong adhesive force between the powder and the mold, leading to difficulties in ejection.
IV. Measures to Address Tungsten Carbide Compaction Issues
- Strengthen Powder Quality Control: Ensure that the quality of tungsten carbide powder meets standards, reducing impurities and pores.
- Optimize Mold Design: Reasonably design the mold’s cavity, vent holes, ejection taper, and other structures to improve powder filling and compaction effects.
- Control Compaction Process Parameters: Select appropriate compaction pressure, holding time, and other parameters based on product requirements to ensure stable compaction processes.
- Regularly Maintain and Inspect Molds: Regularly maintain and inspect molds to ensure their precision and service life.
- Enhance Operator Training: Improve the skill level of operators to reduce the impact of human factors on the compaction process.
V. Conclusion
The common issues encountered in the tungsten carbide compaction process, including uneven compaction density, compaction cracks, dimensional deviations, and difficulties in ejection from the mold, stem from various factors such as powder quality, mold design, and compaction process parameters. By strengthening powder quality control, optimizing mold design, precisely controlling compaction process parameters, and other measures, these issues can be effectively addressed, thereby enhancing the quality and performance of tungsten carbide products. Simultaneously, enhancing operator training and regularly maintaining and inspecting molds are also crucial for ensuring stable tungsten carbide compaction processes and product quality.
Our factory business: carbide parts, mold parts, medical injection molds, precision injection molds, teflon PFA injection molding, PFA tube fittings. email: [email protected],whatsapp:+8613302615729.