Causes of Deformation in Tungsten Carbide Products
Introduction In the field of industrial production, tungsten carbide, as a high – performance hard alloy material, has been widely used due to its high hardness, excellent wear resistance, and […]
Introduction
In the field of industrial production, tungsten carbide, as a high – performance hard alloy material, has been widely used due to its high hardness, excellent wear resistance, and outstanding impact resistance. However, during the processing and use of tungsten carbide products, deformation sometimes occurs. This not only affects the appearance and performance of the products but may also cause damage to the equipment. This article will conduct a comprehensive analysis of the causes of deformation in tungsten carbide products to better understand and solve this problem.
Main Causes of Deformation in Tungsten Carbide Products
Influence of Carbon Gradient
During the processes of dewaxing, presintering, and sintering of tungsten carbide, the carbon content in the product changes, forming a carbon gradient. In an H₂ sintering atmosphere, if the concentration of CxHy compounds is too high and there is an excessive amount of carbon in the filler, especially for large products and those with a “long and flat” shape, the “decarburization” or “carburization” of different parts of the product is uneven. This leads to differences in the sequence and magnitude of shrinkage in different parts, resulting in deformation and bending of the product. In addition, during vacuum sintering, if the pressure inside the furnace is too high, carburization may occur in the parts of the tungsten carbide product close to the graphite crucible, further exacerbating the formation of the carbon gradient.
Our factory business: carbide parts, mold parts, medical injection molds, precision injection molds, teflon PFA injection molding, PFA tube fittings. email: [email protected],whatsapp:+8613302615729.
Influence of Cobalt Gradient
During the vacuum sintering process of tungsten carbide, the wettability of cobalt on the surface of the graphite crucible and its affinity with the product affect the distribution of cobalt liquid within the product. If the wettability of cobalt on the surface of the graphite crucible is poor and the affinity decreases, the cobalt liquid in the product will move upwards. This increases the surface tension on the upper surface of the product and decreases the surface tension on the lower surface, causing the product to bulge upwards. Conversely, if the wettability of cobalt on the graphite crucible is good and the affinity between the cobalt liquid and the crucible increases, the cobalt liquid will move downwards, increasing the surface tension on the lower surface of the alloy and making the product concave downwards. These changes caused by the cobalt gradient can all lead to deformation of the tungsten carbide product.
Influence of Temperature Gradient
After cobalt is heated and melted, it usually flows towards the high – temperature area. That is, the part of the product with a higher temperature will have an increased cobalt content. The greater the change in the temperature gradient, the greater the gradient in cobalt distribution, and the more severe the deformation of the product will be. In addition, the non – uniformity during the heating and cooling processes can also lead to the formation of a temperature gradient, which in turn triggers product deformation.
Influence of Density Gradient in the Pressed Product
During the pressing process of tungsten carbide, due to factors such as force attenuation, uneven material loading, uneven bulk density of the mixture, and the complex shape of the product, a density gradient will be formed within the tungsten carbide product. The parts with higher density have less shrinkage, while the parts with lower density have more shrinkage. Therefore, this affects the deformation and bending of the product.
Influence of Improper Boat Loading and Coefficient of Shrinkage
Improper boat loading and the coefficient of shrinkage are also important factors that lead to deformation of tungsten carbide products. Improper boat loading may cause uneven stress on the product during the sintering process, thereby causing deformation. Moreover, differences in the coefficient of shrinkage can also lead to dimensional changes in the product during processing and use.
Other Factors Causing Deformation of Tungsten Carbide Products
In addition to the above – mentioned main causes, there are some other factors that may also lead to deformation of tungsten carbide products, such as the composition and purity of the material, the rationality of the processing technology, and the precision and stability of the equipment. Although these factors have a relatively small impact on deformation, they cannot be ignored in actual production.
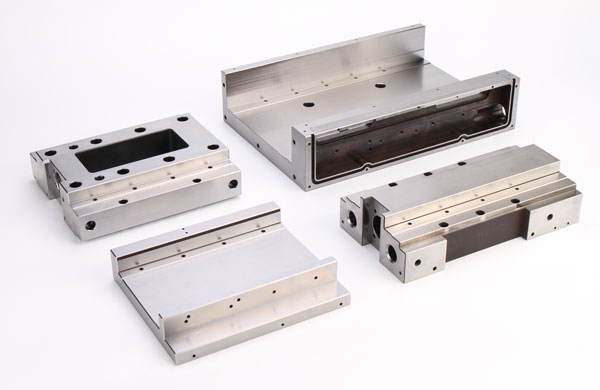
Solutions to the Deformation of Tungsten Carbide Products
Optimize the Production Process
By precisely adjusting parameters such as sintering temperature, pressure, and time, the production process can be optimized to reduce the formation of carbon gradients, cobalt gradients, and temperature gradients. For example, reasonably controlling the sintering temperature and time can make the distribution of carbon and cobalt in different parts of the product more uniform; adjusting the pressure parameters can avoid product deformation caused by uneven pressure.
Improve Equipment Precision and Stability
Using high – precision and high – stability production equipment can ensure uniform stress and dimensional stability of the product during the processing process. Regularly maintain and calibrate the equipment to promptly detect and solve existing problems to ensure the normal operation of the equipment.
Strengthen Material Quality Control
Strictly screen and test raw materials to ensure that the composition and purity of the materials meet the requirements. Establish a strict raw material inspection system, conduct chemical composition analysis and physical performance tests on each batch of raw materials, and only use materials that meet the standards for production.
Improve Boat Loading Method and Control of Shrinkage Coefficient
Optimize the boat loading method to ensure uniform stress on the product during the sintering process. Reasonable boat loading layouts and support methods can be adopted to avoid product deformation due to uneven stress. At the same time, by studying and controlling the coefficient of shrinkage, reduce the dimensional changes of the product during processing and use. For example, during the product design stage, consider the influence of the coefficient of shrinkage and reasonably design the size and shape of the product.
Conclusion
Deformation of tungsten carbide products is a complex problem involving the combined effects of multiple factors. Through in – depth analysis of factors such as the carbon gradient, cobalt gradient, temperature gradient, density gradient in the pressed product, improper boat loading, and the coefficient of shrinkage, we can have a more comprehensive understanding of the causes of deformation in tungsten carbide products. In actual production, we can take a series of measures, such as optimizing the production process, improving equipment precision and stability, strengthening material quality control, and improving the boat loading method and control of the shrinkage coefficient, to effectively reduce the deformation of tungsten carbide products and improve product quality and stability.
A professional tungsten carbide processing manufacturer – Dongguan Yize Mold provides high – quality tungsten carbide molds, tungsten carbide processing, tungsten carbide rollers, tungsten carbide blades, cemented carbide, tungsten carbide punches, and other products. If you have related needs, please feel free to call +86 13302615729 (also available on WeChat and Whatsapp), and we will provide you with more detailed information.