Position > > BLOG
Causes and Solutions for Easy Fracture of Punches
October 04, 2024
view: 58
- Cause: The closing height is set too low, resulting in the punch cutting into the blade section excessively.
Solution: Adjust the closing height to ensure an appropriate length of the punch blade. - Cause: Improper material positioning causes the tungsten carbide punch to cut unilaterally during punching, leading to fracture due to uneven force distribution.
Solution: Adjust the material positioning or optimize the feeding device. - Cause: Waste material in the lower mold blocks the blade, causing the punch to break.
Solution: Enlarge the blanking hole to ensure smooth material flow. - Cause: The fixed part (clamp plate) of the punch is offset from the guiding part (striking plate).
Solution: Repair or re-cut the insert block to ensure smooth vertical movement of the punch. - Cause: Poor guidance of the striking plate results in unilateral force on the punch.
Solution: Re-adjust the clearance of the striking plate to ensure accurate guidance. - Cause: The punch blade is too short, interfering with the striking plate.
Solution: Replace the punch with a new one, increasing the length of the blade section. - Cause: The punch is not securely fixed, allowing vertical movement.
Solution: Re-secure the punch to ensure it remains stable. - Cause: The cutting edge of the punch is not sharp.
Solution: Re-sharpen the cutting edge to restore its sharpness.
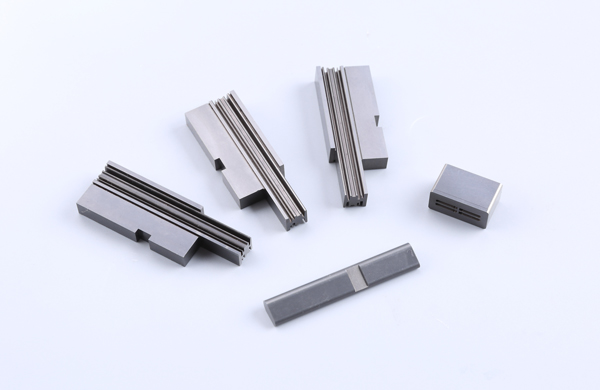