An In-depth Analysis of Tungsten Carbide Punch Materials
In the realm of precision manufacturing, tungsten carbide punches play an indispensable role with their exceptional performance. Today, we delve into the materials that make up tungsten carbide punches, unveiling […]
In the realm of precision manufacturing, tungsten carbide punches play an indispensable role with their exceptional performance. Today, we delve into the materials that make up tungsten carbide punches, unveiling their diverse classifications and unique advantages.
The Art of Classifying Tungsten Carbide Punches by Material
Our factory business: carbide parts, mold parts, medical injection molds, precision injection molds, teflon PFA injection molding, PFA tube fittings. email: [email protected],whatsapp:+8613302615729.
Distinguished by Grain Size: In the world of tungsten carbide punches, the subtle differences in grain size dictate their performance. We categorize them into standard cemented carbide punches, fine-grained cemented carbide punches, and ultrafine-grained cemented carbide punches, each tailored to meet varying industrial needs and precision requirements.
Defined by Chemical Composition: Digging deeper into chemistry, tungsten carbide punches can be further divided into tungsten carbide-based and titanium carbide-based categories. Within the tungsten carbide-based family, YG (tungsten-cobalt), YT (tungsten-cobalt-titanium), and YW (with added rare carbides) each possess distinct characteristics. They harness tungsten carbide (WC), titanium carbide (Tic), niobium carbide (NbC), among others, as core components, complemented by cobalt (Co) as the metal binder, collectively orchestrating a symphony of wear resistance and strength. On the other hand, titanium carbide-based cemented carbides, with Tic taking center stage, paired with molybdenum (Mo) and nickel (Ni) as metal binders, exhibit a different set of performance attributes.
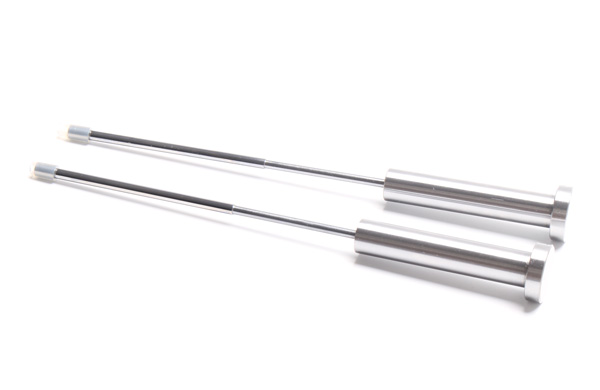
Tungsten Carbide Punches in Cold Working Processes: The Dual Challenge of Wear Resistance and Deformation Resistance
In the broad stage of cold working processes, from punching, shearing to drawing, cold forging, cold extrusion, cold rolling, and powder compaction, each step bears witness to the intense mechanical interplay and sliding contact between tungsten carbide punches and the materials being processed. In this contest, the hardness of the tungsten carbide punch emerges as the pivotal factor. It not only endows the punch with outstanding wear resistance but also, even under the same hardness conditions, demonstrates superior resistance to plastic deformation compared to low-alloy punches. However, this hardness comes with a subtle trade-off in machinability.
Customized Solutions: A Range of High-quality Tungsten Carbide Punches
To cater to the unique demands of different applications, materials being processed, and product types, we have carefully selected a series of high-quality steels to craft your tungsten carbide punches. These punches not only excel in wear resistance and deformation resistance but also balance toughness against chipping and cracking, possess excellent cutting and grinding properties, and ensure stable heat treatment characteristics, guaranteeing precision and efficiency in every punching operation.
In summary, the material selection and design of tungsten carbide punches represent a fusion of science and art, an unwavering pursuit of ultimate performance. On your production line, they will serve as the key to unlocking high-quality products.